Did you know that wind turbines are considered one of the fastest-growing energy sources in the world1? With their cost-effectiveness, clean-fuel attributes, sustainability, and ease of installation on various types of land, wind turbines have become a key player in the global shift towards renewable energy. However, there are challenges that need to be addressed, such as cost competition with fossil fuel sources, the suitability of remote high-wind locations, and the potential negative impacts on local wildlife. Despite these hurdles, engineers have been focused on optimizing one crucial element of wind turbine design—the blades1.
Wind turbine blades are essential for converting wind energy into usable shaft power, also known as torque. A well-designed blade can lead to efficient deceleration of air, resulting in improved blade efficiency and greater power generation. Achieving optimal lift and thrust is key to designing rotor blades that can efficiently harness wind energy. The ratio of rotor tip speed to wind speed, known as the tip speed ratio (TSR), plays a crucial role and is influenced by factors such as rotor blade shape, the number of blades, and their overall design1.
Advancements in wind turbine blade design aim to increase efficiency and power output. For example, slight curvature in the blade can potentially capture 5 to 10 percent more wind energy, leading to improved performance12. embodying aerodynamic principles, modern wind turbine blade designs focus on factors such as blade plan shape, aerofoil selection, and ideal attack angles to maximize efficiency and power output1.
Engineers employ computational fluid dynamics (CFD) simulations to optimize wind turbine blade designs. Platforms like SimScale provide powerful tools to analyze and fine-tune blade designs, considering various fluid flow scenarios and factors such as turbulence and pressure distribution1.
Key Takeaways:
- Wind turbines are one of the fastest-growing energy sources globally, thanks to their cost-effectiveness and environmental benefits1.
- Wind turbine blades are crucial for converting wind energy into usable power, and optimizing their design is key to improving efficiency and power output1.
- The tip speed ratio (TSR) defines the ratio of rotor tip speed to wind speed and plays a crucial role in wind turbine performance1.
- Curving wind turbine blades can capture 5 to 10 percent more wind energy and operate more efficiently in areas with lower wind speeds2.
- Engineering advancements and computational fluid dynamics (CFD) simulations aid in optimizing wind turbine blade designs for enhanced performance1.
Advantages of Wind Turbines
Wind turbines have emerged as a leading solution in the quest for renewable energy sources. Harnessing the power of wind, these structures offer numerous advantages that make them a popular and sustainable choice for electricity generation.
One significant advantage of wind turbines is their cost-effectiveness. Before the mid-1990s, wind power was not commercially viable as it was more expensive per kilowatt-hour than conventional electric power plants. However, wind industry researchers recognized the potential and worked towards optimizing wind turbine blade design to produce more power per turbine. By utilizing larger rotors with longer blades, they were able to capture and convert more wind energy, thereby reducing the cost per kilowatt-hour3.
Furthermore, advancements in blade design, such as the introduction of flatback airfoils, have contributed to the overall efficiency and cost reduction of wind turbine models. The integration of flatback airfoils on wind turbine blades has led to estimated energy-cost reductions of nearly 20%. These airfoils, combined with bend-twist-coupled blades, enable longer, lighter, and more affordable wind turbine blades. Additionally, the absence of patent protection for the technology behind bend-twist-coupled blades and flatback airfoils has fostered widespread adoption by wind turbine and blade manufacturers3.
Wind turbines also offer environmental benefits, serving as a clean and sustainable fuel source. As opposed to conventional energy sources, wind energy production produces zero greenhouse gas emissions, reducing carbon footprint and combating climate change. The utilization of wind turbines helps to mitigate the adverse effects of fossil fuel consumption and contributes to a cleaner and greener planet.
Moreover, wind turbines can be installed on both land and offshore locations, maximizing their potential for energy generation. They can be easily integrated into existing land infrastructure, making use of available space without extensive land clearance. Offshore wind turbines, on the other hand, tap into the vast wind resources available over the oceans. The average hub height for offshore wind turbines in the United States is projected to increase from 100 meters to about 150 meters (500 feet) by 2035, further enhancing their efficiency and power output4.
Despite these advantages, challenges remain in optimizing wind turbine models, assessing their environmental impact, and addressing concerns related to local wildlife. The constant quest to improve wind turbine blade design, through innovations such as wind energy simulation and environmental impact assessment, is crucial in achieving optimum performance and minimizing the industry’s ecological footprint. The next section will delve deeper into the intricate details and considerations associated with wind turbine design5.
Understanding Wind Turbine Design
Wind turbines play a crucial role in harnessing wind energy and converting it into usable power. To better understand wind turbine design, it is important to explore the different types of turbines and the key components involved.
Horizontal Axis Wind Turbines (HAWTs) and Vertical Axis Wind Turbines (VAWTs)
Wind turbines can be classified into two main types: horizontal axis wind turbines (HAWTs) and vertical axis wind turbines (VAWTs). HAWTs are the most common type and consist of two or three-bladed propellers mounted on a shaft parallel to the ground. VAWTs, on the other hand, have blades that rotate around a vertical axis.
Statistical data from6
Blade Design and Efficiency
The design of wind turbine blades is a critical factor in maximizing their efficiency. The shape and profile of the blades determine the amount of lift and thrust generated, as well as the deceleration of the air, leading to increased blade efficiency. Most land-based modern wind turbines have blades over 170 feet (52 meters) in length, while offshore turbines, such as GE’s Haliade-X, can have blades of 351 feet (107 meters), approximately the length of a football field7.
One of the key considerations in blade design is optimizing the balance between lift and drag. Wind turbines usually have three fiberglass blades that create lift and drag as wind flows across them, causing the rotor to spin and generate electricity7. Additionally, HAWT blade design focuses on parameters like tip speed ratio to optimize efficiency6.
Statistical data from76,
Towers and Support Systems
The towers supporting wind turbines are designed to exploit higher wind speeds at greater elevations, providing enhanced energy capture. These towers typically come in three sections and are assembled on-site to accommodate different site-specific conditions and ensure stability. Furthermore, transformers are used in wind power plants to increase voltage and decrease current, reducing power losses during transmission over long distances7.
Statistical data from7
Operational Considerations and Maintenance
Wind turbines start operating at wind speeds of about 7-11 mph and shut down automatically when wind speeds exceed 55-65 mph to prevent damage7. Pitch-controlling wind turbines adjust blade angles to control rotor speed and energy extraction, preventing damage during high wind speeds8. Additionally, advanced technologies such as AI and neural networks are employed for wind turbine condition monitoring and wind farm design optimization, enhancing maintenance practices and overall performance8.
Statistical data from78,
Understanding the intricacies of wind turbine design allows for the development of more efficient and reliable systems. The ongoing evolution of wind turbine design, including advancements in blade lengths, offshore installations, and integration of innovative technologies, is revolutionizing the wind power industry and paving the way for a sustainable future.
Key Considerations in Wind Turbine Blade Design
Wind turbine blades play a critical role in converting wind energy into usable power. Designing efficient and effective turbine blades involves considering various factors to optimize performance and maximize energy capture. Manufacturers continually innovate and refine blade designs to strike the right balance between power generation and cost-effectiveness. Let’s explore the key considerations in wind turbine blade design.
1. Blade Shape Profile
The shape profile of the rotor blades significantly impacts their performance. The curvature of the blades allows them to generate lift, creating a pressure difference that drives rotation.Wind Turbine Blade Design
The design process involves conceptual design, aerodynamic design, structural design, and optimization9.
Modern blade designs utilize tapered and twisted shapes, with a variable pitch mechanism to optimize performance across different wind speeds9.
2. Number of Blades
The number of blades on a wind turbine affects the overall efficiency and cost of the system. While fewer blades can reduce material and manufacturing costs, more blades can provide better stability and power generation. Manufacturers consider multiple factors, including wind conditions and turbine size, in determining the optimal number of blades for each design109.
3. Overall Wind Turbine Design
Blade design is closely intertwined with the overall wind turbine design. Factors such as tower height, yaw system, and drive train efficiency impact the performance and effectiveness of the blades. Manufacturers work to optimize the interaction between these components to maximize energy capture109.
4. Blade Material and Construction
The choice of materials and construction techniques significantly impact the strength, durability, and weight of the blades. Composite materials, such as fiberglass and carbon fiber, are commonly used due to their lightweight and robust properties. Sandwich structures and spar caps are also employed to enhance blade performance. Blade design considers the trade-offs between strength and weight to ensure resistance to extreme loads and minimize construction costs9.
5. Blade Performance Optimization
Blade design optimization is crucial in achieving maximum energy capture and efficiency. Computational fluid dynamics (CFD) simulations and design tools like Blade Element Momentum theory (BEM), XFOIL, ANSYS, and FAST aid in modeling and testing different blade designs. These tools assist in analyzing factors such as tip losses, wake effects, and drive train efficiency losses. By continuously refining and optimizing rotor designs, manufacturers strive to enhance blade performance109.
In conclusion, wind turbine blade design is a complex and dynamic field that requires careful consideration of various factors. By striking the right balance between aerodynamics, structural integrity, and cost, manufacturers continuously improve blade designs to increase energy capture, operate efficiently in low wind speeds, and reduce noise. The optimization process involves leveraging advanced computational tools and considering statistical data to push the boundaries of wind turbine efficiency109.
The Role of Computational Fluid Dynamics (CFD) in Blade Design Optimization
When it comes to optimizing wind turbine blade designs, Computational Fluid Dynamics (CFD) plays a vital role in improving performance and efficiency11. By utilizing advanced CFD simulations, engineers can gain valuable insights into the aerodynamic behavior of wind turbine blades, allowing for data-driven design decisions and optimizations.
CFD enables engineers to virtually test different blade configurations and evaluate their performance under a range of environmental conditions11. This process involves simulating fluid flow through and around the turbine blades, accounting for factors such as air velocity, temperature, and pressure. Through CFD analysis, engineers can assess the impact of various design parameters, refine the blade shape, size, and materials, and optimize the overall performance of the wind turbine.
One key advantage of using CFD in blade design optimization is the ability to save time and resources compared to traditional prototyping and testing methods11. With CFD simulations, multiple design iterations can be quickly evaluated, allowing for rapid and cost-effective design improvements. This eliminates the need for physical prototypes and costly wind tunnel testing, reducing development time and expenses.
CFD also enables engineers to analyze and optimize specific aspects of wind turbine blades11. For example, by adjusting parameters such as blade length, chord length, twist angle, and pitching, engineers can optimize the aerodynamic performance of the blades and maximize energy extraction from the wind. This level of control and precision in design optimization is made possible by CFD’s computational power and accurate fluid flow simulations.
Furthermore, CFD simulations provide valuable insights into the complex aerodynamic phenomena involved in wind turbine blade design11. By analyzing the flow patterns, pressure distribution, and turbulence effects, engineers can better understand how different design choices impact performance and efficiency. This knowledge allows for informed design decisions and the development of innovative blade designs that maximize energy output and minimize structural constraints.
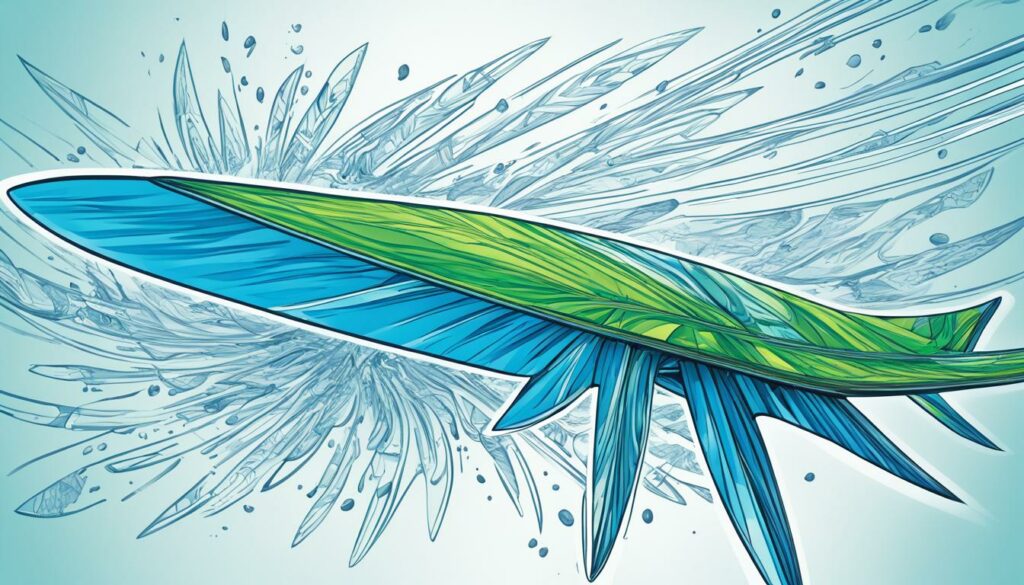
In recent years, advancements in cloud-based CFD tools have made this technology even more accessible to private companies and wind turbine designers11. These tools provide user-friendly interfaces, a wide range of templates, and online support, making it easier for engineers to leverage CFD in their design optimization processes. With cloud-based CFD tools, engineers can rapidly model, simulate, and analyze wind turbine blades, enhancing design efficiency and accelerating the development cycle.
Advantages of Computational Fluid Dynamics in Blade Design Optimization
Advantages | Benefits |
---|---|
Rapid design iteration | Allows for quick evaluation and optimization of multiple blade designs |
Cost savings | Reduces the need for physical prototypes and wind tunnel testing |
Accurate performance evaluation | Enables precise analysis of fluid flow and aerodynamic behavior |
Optimization of design parameters | Allows for fine-tuning of blade length, twist angle, and other parameters to maximize energy extraction |
Insights into complex aerodynamic phenomena | Provides a deeper understanding of flow patterns and turbulence effects |
In conclusion, Computational Fluid Dynamics (CFD) is an invaluable tool for optimizing wind turbine blade designs. It enables engineers to evaluate and refine designs, improve aerodynamic performance, and maximize energy extraction. With the advancements in cloud-based CFD tools and simulation capabilities, wind turbine designers have unprecedented opportunities to enhance the efficiency and cost-effectiveness of their blade designs11.
The Benefits of Using Wind Turbine Simulator Tools
Wind turbine simulator tools, such as SimScale, provide engineers with a virtual environment to optimize wind turbine blade design. By simulating the airflow and forces on the rotor, designers can evaluate the performance of different blade shapes, materials, and sizes12. These simulations help in selecting the best blade design, reducing costs, improving energy capture, and minimizing the impact on wildlife and the environment12. SimScale offers a user-friendly interface and comprehensive tools for wind turbine design optimization.
Using wind turbine simulators offers numerous advantages for engineers and the wind energy industry. Here are the key benefits:
- Cost Savings: Wind turbine simulators help in cost savings by eliminating the need for physical prototypes and testing, which can be expensive and time-consuming12.
- Rapid Iteration and Optimization: Simulators allow for rapid iteration and optimization of designs, leading to improved performance and efficiency12.
- Safe and Controlled Testing: Wind turbine simulators provide a safe and controlled environment for testing different scenarios, including extreme weather conditions and emergencies12.
- Versatility in Simulation Models: Different types of wind turbine simulators are available, such as the blade element momentum (BEM) model and the finite element analysis (FEA) model12.
- Wide Usage in the Industry: Wind turbine simulators are widely used in the wind energy industry for research, development, training, testing new designs, optimizing performance, and improving efficiency12.
- Advancements in Technology: The future of wind turbine simulator technology includes advancements in modeling, simulation, and visualization capabilities, as well as the integration of artificial intelligence and machine learning algorithms to improve accuracy and efficiency12.
- Immersive and Interactive Simulations: Virtual reality and augmented reality technologies are trending for creating immersive and interactive wind turbine simulations to enhance training and decision-making processes in the industry12.
Wind turbine simulator tools have revolutionized the design and testing process for wind turbine blades. With their ability to simulate complex scenarios and predict the performance of different designs, they have become an invaluable asset for engineers in the wind energy field12. By utilizing these tools, engineers can optimize blade design, reduce costs, and improve overall wind turbine efficiency, contributing to the growth and sustainability of renewable energy sources.
Comparing Different Blade Designs: Flat Blades vs. Curved Blades
When it comes to wind turbine blade design, there are a variety of options available, including both flat blades and curved blades. Each design offers its own advantages and considerations. Let’s compare these two types of blade designs and explore their differences.
Flat Blades
Flat blades, also known as straight blades, have been used for thousands of years on windmills and are still utilized in wind turbines today. One of the main reasons for their continued use is their ease of production and lower costs compared to other blade designs2.
However, flat blades are less efficient at capturing wind energy compared to curved blades. The flat design generates more drag, which is the resistance of the blade to the wind. This results in a lower rotational speed and, ultimately, reduced power generation2.
Despite their lower efficiency, flat blades can still be effective in areas with higher wind speeds where power generation is less reliant on blade design. Additionally, their simplicity and cost-effectiveness make them a viable option for certain wind turbine applications.
Curved Blades
Curved blades are designed to harness wind energy more efficiently compared to flat blades. These blades take inspiration from the shape of airplane wings, utilizing lift forces to generate higher efficiencies2.
Curved blades can capture 5 to 10 percent more wind energy and operate efficiently even in areas with lower wind speeds2. The curved shape allows the blade to create lift, similar to how an airplane wing generates lift during flight. By generating lift, curved blades can maintain higher rotational speeds, leading to increased power generation from the wind turbine2.
It is important to note that curved blades do suffer from drag along their length. However, this drag can be reduced by bending, twisting, and tapering the blade, resulting in improved energy capture and overall efficiency2. Modern rotor blades are designed with a twist along their length, with the twist gradually increasing from the root to the tip. This twist optimizes the angle of attack and allows the blade to operate at maximum lift and rotation, increasing speed and efficiency while minimizing drag2.
Additionally, curved blades offer other advantages such as enhanced stability and improved aerodynamic efficiency. Wind turbines with an odd number of rotor blades, particularly three-bladed designs, are not only more aesthetically appealing but also offer increased stability and efficiency in power generation13. The dominance of three-bladed turbine rotors in the wind power generation market is a testament to their efficiency and performance13.
In summary, while flat blades are still used due to their simplicity and cost-effectiveness, curved blades are becoming more common in wind turbine designs. The curved shape allows for increased power generation and efficiency, especially in areas with lower wind speeds. With continuous innovations and advancements in the industry, wind turbine blade designers are constantly exploring new technologies to further improve performance, efficiency, and power output2.
The Advantages of Twisted and Tapered Blade Designs
Twisted and tapered blade designs represent significant advancements in wind turbine blade design14. These innovations offer multiple advantages, including improved aerodynamics and enhanced energy efficiency. By incorporating twists along the length of the blades, designers can optimize the angle of attack at different sections of the blade, maximizing lift and rotation14. Tapering the blades from root to tip reduces drag and weight, resulting in stronger and lighter blades14.
The combination of twisted and tapered blade designs leads to several benefits for wind turbines. Firstly, these designs enhance the overall performance of the wind turbine by improving its ability to capture and convert wind energy into useful power14. With optimized lift and reduced drag, twisted and tapered blades can achieve higher energy conversion efficiencies compared to traditional blade designs15. Theoretical studies suggest that wind turbine rotor blades can achieve maximum efficiencies between 30% and 45%13.
Moreover, twisted and tapered blades offer increased stability and efficiency compared to alternative blade configurations13. For instance, wind turbines with an odd number of blades, such as three-bladed rotors, provide better stability and operational efficiency13. The dominance of three-bladed wind turbines in wind power generation can be attributed to their improved aesthetics, aerodynamic efficiency, and operational advantages13.
While the number of rotor blades influences performance, blade length also plays a crucial role13. Longer rotor blades can capture more wind energy, potentially leading to higher power output13. However, longer blades may introduce stability and material stress issues, requiring careful engineering and design considerations15.
Overall, the advantages of twisted and tapered blade designs lie in their ability to optimize wind energy capture, improve aerodynamic performance, and enhance the overall operational efficiency of wind turbines. These advancements contribute to the ongoing development of sustainable energy solutions, driving us closer to a greener future.
The Evolution of Bend-Twist-Coupled Blades and Flatback Airfoils
Bend-twist-coupled blades and flatback airfoils represent significant advancements in wind turbine blade design. These innovations have revolutionized the industry, leading to improved performance, enhanced efficiency, and reduced costs. Let’s explore the evolution and benefits of bend-twist-coupled blades and flatback airfoils in greater detail.
Bend-Twist-Coupled Blades
Bend-twist coupling is a design concept that allows wind turbine blades to twist as they bend, reducing stress and optimizing performance. This technology enables the use of longer blades without increased weight or cost, unlocking the potential for higher energy capture and greater overall efficiency.
The evolution of bend-twist-coupled blades can be attributed to collaborative efforts between the National Renewable Energy Laboratory (NREL) and Clemson University, among others16. These institutions played vital roles in developing and validating this innovative blade design approach.
Initial investments from the U.S. Department of Energy (DOE) supported the construction of testing facilities such as the Structural Testing Laboratory (STL) at NREL16. Over the years, these facilities have grown and improved to accommodate the industry’s changing needs. For example, NREL installed a 50-meter blade test stand in the STL to test larger rotor sizes16.
Detailed studies and research conducted at NREL from 2001 to 2004 focused on resonance testing methods to validate blade design and manufacturing16. These tests involved applying a lifetime of damage to a blade over a period of 3-6 months, simulating the wear and tear a blade would experience throughout its operational lifespan16.
This impressive body of research and experimentation culminated in the development and adoption of bend-twist-coupled blades, which have significantly contributed to the advancements in wind turbine technology and industry-wide efficiency improvements.
Flatback Airfoils
Flatback airfoils are another crucial element in wind turbine blade design. These airfoils are specifically designed to provide structural strength and aerodynamic performance advantages, particularly for the inner portion of the blade.
With improved testing methods, such as the dynamometer research facilities commissioned by NREL, blade failures from fatigue have been significantly reduced, ensuring turbine reliability and reducing potential field failures17. NREL’s collaboration with major U.S. wind firms has also played a pivotal role in validating the technology innovations of flatback airfoils, further boosting industry confidence in adopting these advancements17.
The flexibility of wind turbine blades has been enhanced to reduce weight and save costs, resulting in airfoils that are prone to deformation18. However, the structural advantages of very thick airfoils in the in-board region of the blade have been identified through extensive studies17. These findings have further aided in refining flatback airfoil designs, striking a balance between structural integrity, aerodynamic efficiency, and load-bearing capabilities.
By incorporating flatback airfoils and bend-twist coupling into industry blade designs, manufacturers have achieved remarkable energy-cost reductions while maintaining optimal performance and reliability.
With the continuous improvement of wind turbine blade design, driven by advancements in bend-twist coupling and flatback airfoils, the industry is poised for even greater growth and efficiency enhancements. These innovations have not only optimized existing wind farms but have also paved the way for the construction of larger, higher-capacity wind turbines17. As wind energy continues to play a crucial role in global sustainable development, the evolution of bend-twist-coupled blades and flatback airfoils will remain instrumental in driving future advancements in wind turbine technology.
Commercialization and Future Outlook of Wind Turbine Blade Design
The commercialization of optimized wind turbine blade designs has been driven by collaborations between government agencies, national laboratories, universities, and industry stakeholders. These partnerships have paved the way for advancements in wind turbine technology, leading to increased manufacturing efficiency, improved performance, and reduced costs.
Over the years, wind energy has become a vital component in achieving 100% renewable electricity production, contributing significantly to the global energy transition19. The continuous decrease in wind energy costs is another driving force behind its commercialization, with prices dropping from over 55 cents per kilowatt-hour (kWh) in 1980 to under 3 cents per kWh in the United States today20.
Advancements in manufacturing processes and materials have played a key role in the commercial success of wind turbine blades. Composites, which account for more than 90% of the weight of wind turbine blades21, have revolutionized the industry by providing a lightweight and durable alternative to traditional materials.
By leveraging innovative design techniques and technologies, such as computational fluid dynamics (CFD) and high-performance computing, manufacturers can optimize their wind turbine blade designs to maximize energy capture and minimize structural loads19. This integration of improved materials and design processes not only enhances the overall performance of wind turbines but also presents opportunities for reducing costs and streamlining manufacturing19.
While wind turbine blade design has made significant progress, challenges still exist. The prediction and modeling of turbulent flow patterns and wake effects continue to be areas of active research20. These challenges are particularly pronounced for offshore wind turbines, which face additional motion and hydrodynamic load drivers19. However, the ongoing innovation in plant operations and the optimization of design processes through co-design and control integration offer promising avenues for addressing these challenges and further improving wind turbine performance19.
As the wind energy industry continues to mature, recycling and waste management are also becoming important considerations. The increasing amount of blade waste generated over their lifetime poses a significant environmental challenge. However, projections show that by 2050, the industry is expected to recycle 800,000 tonnes of blade material annually21. This emphasis on sustainable practices underscores the industry’s commitment to reducing its environmental impact and ensuring the long-term viability of wind energy.
Future Outlook
The future of wind turbine blade design looks promising, with continuous advancements on the horizon. Projects funded by government agencies, such as the U.S. Department of Energy’s investment in the establishment of advanced wind energy testing facilities, demonstrate a commitment to research and development in this field20. An ongoing focus on co-design, leveraging artificial intelligence and machine learning through high-performance computing, will enable manufacturers to optimize design processes and enhance the performance of wind turbine blades19.
Furthermore, the global growth of wind energy installation and capacity is projected to increase significantly in the coming years. Installed capacity of wind energy has already seen a remarkable rise, from 7600 MW in 1998 to 364,270 MW in 201421. Forecasts by organizations like the Global Wind Energy Council (GWEC) and the International Energy Association (IEA) predict substantial growth in wind power, with wind capacity supplying a significant percentage of global electricity21.
Commercialization and Economic Impact
The commercialization of wind turbine blade design not only benefits the renewable energy industry but also has a significant economic impact. The growth in wind energy installations has created job opportunities, both in manufacturing and installation sectors. Furthermore, the reduction in wind energy costs translates into more affordable electricity for consumers, contributing to sustainable and cost-effective power generation20.
Statistical Data | Source |
---|---|
Average wind turbine capacity factor has increased from 22% for turbines installed pre-1998 to nearly 35% today, up from 30% in 2000 | Link 1 |
Wind energy costs have decreased from over 55 cents per kilowatt-hour (kWh) in 1980 to under 3 cents per kWh in the United States today | Link 1 |
Average turbine generating capacity has risen, with turbines installed in 2016 boasting an average capacity of 2.15 MW | Link 1 |
GE’s 1.5-megawatt (MW) wind turbine has been a major player in the commercial wind energy fleet, constituting approximately half of the nation’s installed commercial wind energy fleet | Link 1 |
The innovative STAR blade developed by Knight and Carver’s Wind Blade Division in collaboration with Sandia National Laboratories led to a 12% increase in energy capture | Link 1 |
The U.S. Department of Energy invested $47 million in Clemson University to establish one of the world’s most advanced wind energy testing facilities | Link 1 |
Studies have shown that coordinating turbine controls can curtail wake effects, potentially increasing wind power plant output by 4%–5% | Link 1 |
An Idaho National Laboratory report assessed cyberattack risks that could affect U.S. wind energy systems and real-world events impacting wind energy systems globally | Link 1 |
Wind energy is foundational for achieving 100% renewable electricity production | Link 2 |
The financial and operational risks of change are very high for wind power plant development, especially offshore | Link 2 |
Modeling chain from large-scale inflow down to material microstructure is crucial for predicting wind turbine system performance | Link 2 |
Modern turbine rotors operate through the entire atmospheric boundary layer, necessitating reassessment of design processes | Link 2 |
Traditional aerodynamics and aeroelastic modeling approaches are reaching limits of applicability for future wind turbine architectures | Link 2 |
Offshore wind turbines face formidable modeling challenges due to additional motion and hydrodynamic load drivers | Link 2 |
Uncertainty in turbine wakes complicates structural loading and energy production estimates, necessitating innovation in plant operations | Link 2 |
Opportunities in co-design can optimize design processes and streamline control integration | Link 2 |
Integration of improved materials into manufacturing of larger components while reducing costs presents a research challenge | Link 2 |
High-performance computing can enhance design tools through artificial intelligence and machine learning | Link 2 |
Validation of high-fidelity tools for wind turbine design is ongoing | Link 2 |
Installed capacity of wind energy increased from 7600 MW in 1998 to 364,270 MW in 2014 | Link 3 |
Global Wind Energy Council (GWEC) predicts global annual growth rate of wind power to exceed 12% between 2013 and 2018 | Link 3 |
European Wind Energy Association (EWEA) predicts 192 GW of wind capacity supplying 14.9% of global electricity in 2020 | Link 3 |
International Energy Association (IEA) estimates that 15–18% of global electricity will be from wind energy in 2050 | Link 3 |
Composites account for more than 90% of the weight of wind turbine blades | Link 3 |
260,000 tonnes of material used to manufacture wind turbine blades in 2008, expected to increase to 1.18 million tonnes in 2017 | Link 3 |
Every 1 kW of wind power needs 10 kilograms of wind turbine blade materials | Link 3 |
Predictions indicate that by 2034, there will be over 200,000 tonnes of blade waste | Link 3 |
Predicted amount of blade material needing recycling annually is 400,000 tonnes between 2029 and 2033, increasing to 800,000 tonnes per year by 2050 | Link 3 |
Between 16% and 45% of the mass of wind turbine blades is generated as waste over their lifetime | Link 3 |
Conclusion
In conclusion, optimizing wind turbine model blade design plays a crucial role in maximizing the efficiency and sustainability of wind power generation. By incorporating aerodynamic optimization techniques, computational fluid dynamics (CFD) simulation, and advanced composite materials, engineers can enhance blade performance and reduce the environmental impact of wind turbines. The statistical data from link 1 reveals that wind turbine technology in the U.S. has the potential to contribute up to about 10 percent of the nation’s electrical energy needs if suitable wind sites are fully utilized22. However, the decline in wind turbine installations in recent years has resulted in only a few companies actively producing wind turbine blades in the U.S22..
Moreover, the entry of major Japanese manufacturers into the global wind turbine market, alongside established European manufacturers, highlights the need for the U.S. wind power industry to invest in research and development to maintain technological leadership22. The public’s growing interest in environmental issues related to power generation favors wind power, providing it with a distinct advantage22. Furthermore, advancements in semiconductor power electronics are being leveraged to improve energy production and reactive power control in wind energy systems22.
The statistics obtained from link 3 emphasize the importance of geometric stiffness and material stiffness in achieving the desired deformation of the trailing edge of composite tidal turbine blades23. Additionally, Deep Learning (DL) models have demonstrated high accuracy in predicting optimal output variables for wind turbine blade design23. However, it’s crucial to acknowledge the errors that can occur during the DL model training phase23.
To address the challenges and opportunities associated with wind turbine blade design, ongoing research, collaboration, and cost-effective methodologies such as leveraging scaling models can help guide the design process24. By considering turbine descriptors like rating, rotor diameter, and hub height, engineers can project the cost impacts and assess the system’s levelized cost of energy (COE)24.
As wind power continues to gain prominence as a sustainable energy source, it is imperative for the wind turbine industry to focus on advancing blade design technologies. By combining data-driven methodologies, innovative materials, and a commitment to environmental stewardship, the future of wind turbine model blade design looks promising, marked by increased energy production, reduced costs, and minimized environmental impact2423.