As I immerse myself in wind turbine optimization, I've come to realize that mastering aerodynamic forces is essential to revealing the full potential of renewable energy. A single optimized turbine can increase energy production by up to 20%! To get started, I focus on understanding wind turbine aerodynamics, including intricate interactions between blades, hub, and tower. Next, I set up accurate simulations in Ansys, ensuring proper mesh generation and boundary conditions. By preparing geometry and conditions, running and analyzing simulations, and refining turbine design, I can unveil optimum performance. And that's just the beginning – there's much more to explore in the world of wind turbine optimization.
Key Takeaways
- Accurate CFD simulations in Ansys enable wind turbine optimization by capturing complex aerodynamic forces and interactions between blades, hub, and tower.
- High-quality mesh generation and proper boundary conditions are essential for precise flow calculations and reliable simulation results.
- Selecting the appropriate turbulence model and fine mesh resolution are critical for simulating flow behavior and resolving flow patterns and aerodynamic forces.
- Continuous design refinement using CFD analysis and validation against experimental data ensures optimal wind turbine performance under various wind conditions.
- Ansys allows for quick testing and optimization of different design scenarios, enabling the refinement of blade geometry, pitch angles, and tower height for maximum efficiency.
Understanding Wind Turbine Aerodynamics
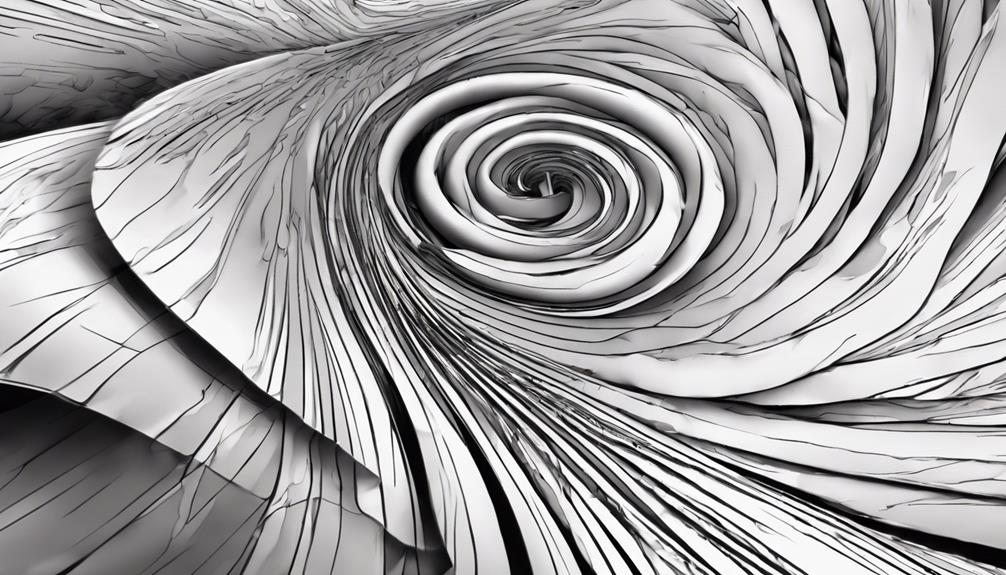
As I delve into the intricacies of wind turbine optimization, I'm reminded that understanding wind turbine aerodynamics is vital to revealing the full potential of these renewable energy powerhouses.
The aerodynamic forces that act on a wind turbine blade are complex and multifaceted, involving interactions between the blade, hub, and tower. CFD analysis plays a pivotal role in uncovering these complex flow patterns, allowing us to visualize and quantify the aerodynamic forces at play.
Setting Up Accurate Simulations
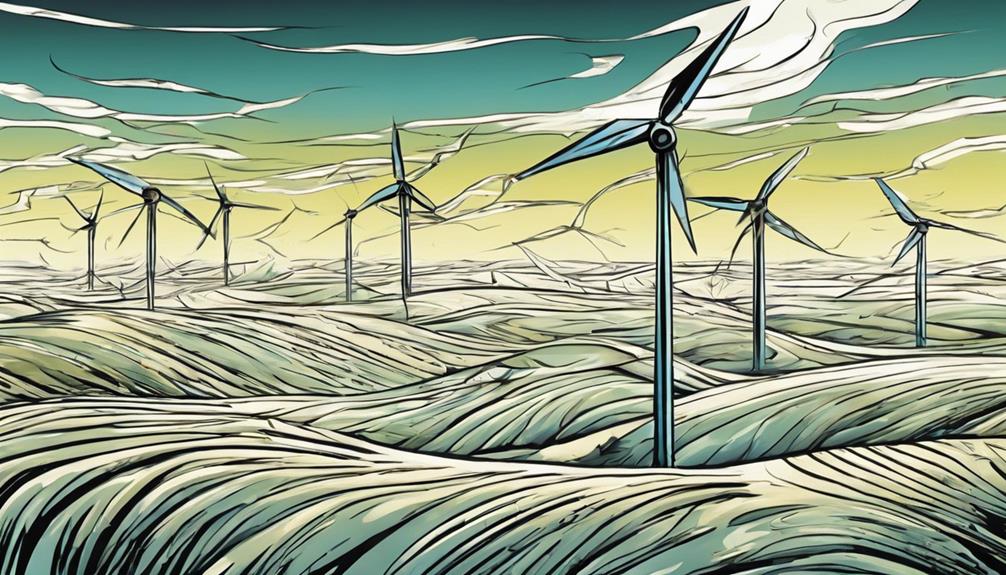
When it comes to wind turbine optimization, I've found that setting up accurate simulations in Ansys is important, and it all starts with proper mesh generation and boundary conditions.
A well-organized mesh is essential for precise flow calculations, and Ansys provides tools to create detailed meshes that accurately represent turbine geometry.
Next, I configure boundary conditions to reflect real-world operating conditions, specifying flow velocity, temperature, and pressure. This guarantees that my simulation results are reliable and representative of actual turbine performance.
Preparing Geometry and Conditions
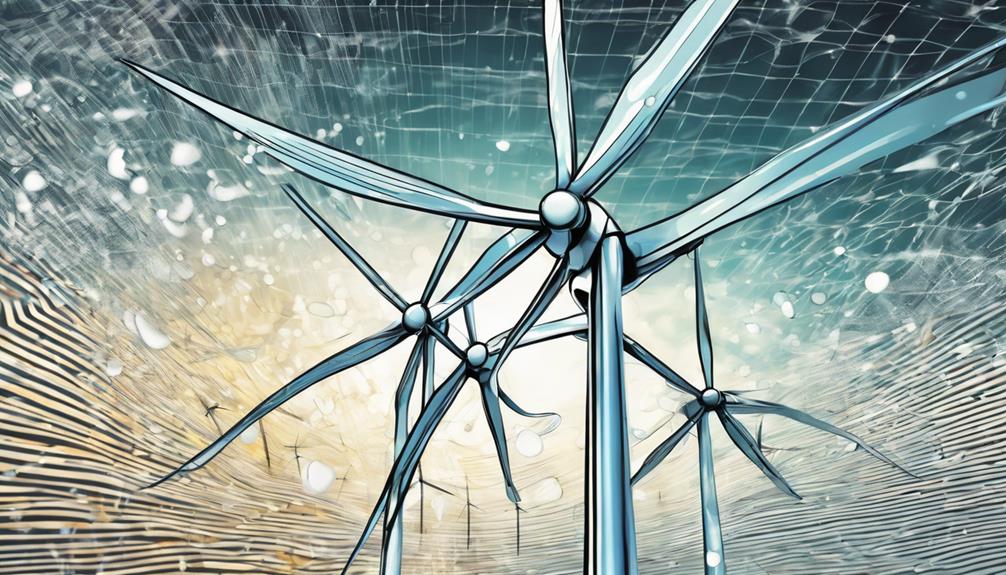
I begin preparing the geometry by generating a high-quality mesh that captures the intricate details of the wind turbine's complex shape, which is vital for accurate CFD analysis.
In Ansys, I create a detailed mesh that represents the turbine's geometry, ensuring that it's fine enough to resolve the flow patterns and aerodynamic forces.
Next, I configure the boundary conditions, specifying the flow velocity, temperature, and pressure that mimic real-world operating conditions.
I also select the appropriate turbulence model, which is pivotal for simulating the complex flow behavior around the turbine.
Running and Analyzing Simulations

Initializing the simulation, I monitor convergence and track key performance metrics to ensure accurate and dependable results.
As the simulation runs, I keep a close eye on the residual plots to guarantee the solution converges. Once converged, I extract key performance metrics such as power output, thrust, and efficiency.
I then validate these results against experimental data or existing simulations to ensure precision. Visualizing the CFD results helps me understand the complex flow patterns and aerodynamic forces around the turbine. I can identify areas of improvement and optimize the design accordingly.
Refining Turbine Design for Optimum
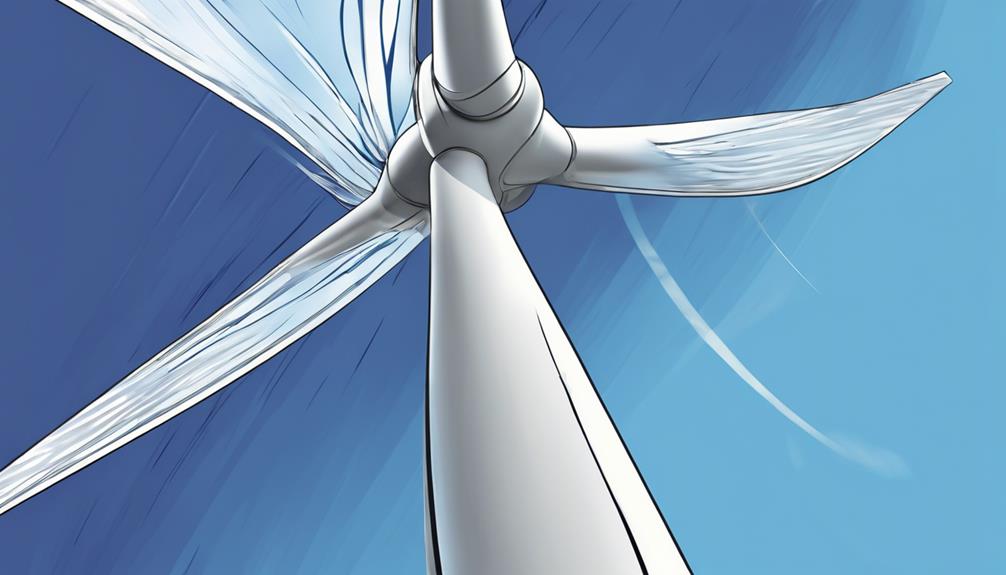
By leveraging the insights gleaned from CFD analysis, I can now refine the wind turbine design to achieve optimum performance. I'll modify the blade geometry, pitch angles, or tower height based on the simulation results. This iterative process allows me to evaluate the effects of different wind conditions and perform parametric studies.
I'll continuously refine the design, using CFD analysis to validate each iteration. With Ansys, I can quickly test and optimize various design scenarios, ensuring that my wind turbine operates at its best. By refining the design, I can increase energy production, reduce costs, and minimize environmental impact.
With each refinement, I'm one step closer to creating a highly efficient wind turbine that harnesses the power of wind effectively.
Frequently Asked Questions
What Is the Ideal Mesh Size for Wind Turbine CFD Simulations?
When it comes to mesh size for wind turbine CFD simulations, I aim for a balance between accuracy and computational efficiency, typically using a mesh size between 1-5 million elements, depending on the turbine's complexity.
Can Ansys CFD Handle Complex Wind Turbine Geometries?
"Yes, I can confidently say that Ansys CFD can handle complex wind turbine geometries. Its advanced meshing capabilities and versatile solver settings allow for accurate simulations of intricate blade shapes and turbine components."
How Do I Account for Turbulence in Wind Turbine CFD Analysis?
"Time to get turbulent In Ansys CFD, I use Reynolds-Averaged Navier-Stokes (RANS) or Large Eddy Simulation (LES) to account for turbulence, ensuring accurate simulations that capture the chaotic dance of wind around my wind turbine design."
What Are the Key Performance Metrics to Extract From CFD Results?
When analyzing CFD results, I extract key performance metrics like torque, power output, and blade loading to evaluate wind turbine efficiency, and then validate these metrics against experimental or field data.
Can Ansys CFD Simulate Wind Turbine Performance in Urban Environments?
"Absolutely, I can harness Ansys CFD to simulate wind turbine performance in urban environments. I'd model complex cityscapes, capturing nuanced wind flows and turbulence around buildings, to optimize turbine placement and efficiency."
How Can Ansys CFD Help in Enhancing Wind Turbines and Power Generation?
Ansys CFD plays a crucial role in boosting power with blades. By using advanced simulation and analysis, Ansys CFD helps in optimizing the design and performance of wind turbines. It enables engineers to improve aerodynamics, reduce energy loss, and enhance power generation, ultimately leading to more efficient and sustainable wind energy production.
Conclusion
As I reflect on my journey with Ansys CFD, I've come to realize that mastering wind turbine optimization is like steering a ship through challenging waters – it requires precision, patience, and a deep understanding of the underlying currents.
With Ansys CFD as my guide, I've been able to chart a course towards more efficient turbine designs, revealing the secrets to harnessing the power of nature.