The internal design of liquid hydrogen transport units plays a crucial role in gas boil-off rates. Features like multi-layer insulation and vacuum-jacketed tanks significantly reduce heat transfer, minimizing energy loss and preventing boil-off gas. Implementing effective heat management systems and understanding thermal stratification further enhance efficiency. You might find it interesting how these factors intertwine to ensure safety and operational integrity in hydrogen transport. There's much more to explore in this fascinating field.
Key Takeaways
- The internal build of vacuum-jacketed tanks minimizes heat leakage, directly reducing boil-off gas production during liquid hydrogen transport.
- Multi-layer insulation enhances thermal efficiency, lowering external heat transfer and subsequently decreasing boil-off rates.
- Effective thermal stratification management within tanks helps to control temperature differences, preventing excessive ullage stratification and gas accumulation.
- Advanced pressure management techniques utilize boil-off gas effectively, reducing unnecessary tank stress and improving overall transport efficiency.
- Regular assessments of tank design and insulation materials are essential for compliance with safety regulations and optimal hydrogen transport performance.
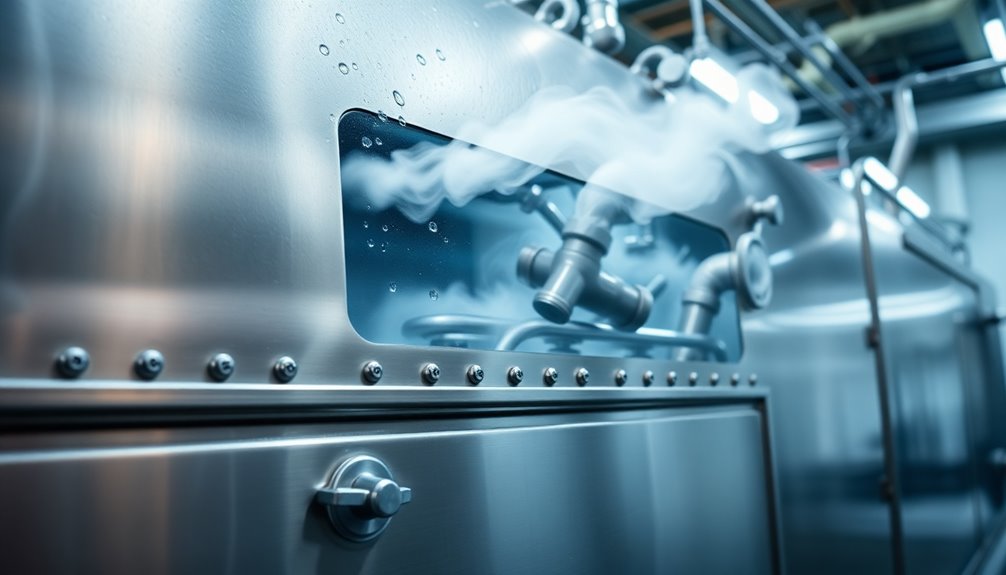
When transporting liquid hydrogen, understanding the connection between internal build and gas boil-off is crucial for optimizing efficiency and safety. Your choice of tank design plays a significant role in this process. Vacuum-jacketed tanks with multi-layer insulation are essential for minimizing heat leakage. By reducing external heat transfer, high-quality insulation can substantially lower boil-off gas production.
Effective heat management systems are vital for maintaining cryogenic conditions. You need to control temperature meticulously to limit boil-off, as even minor heat leaks can drastically impact boil-off rates and overall system efficiency. Advanced technologies, like NASA's Integrated Refrigeration and Storage (IRAS), aim for zero boil-off (ZBO) through sophisticated refrigeration methods. Innovations in insulation materials also contribute to reducing boil-off, enhancing the efficiency of your transport units. Additionally, the development of technology to convert boil-off gas into reusable fuel can further optimize the utilization of this byproduct.
Effective heat management is crucial for cryogenic transport, maximizing efficiency and minimizing boil-off through advanced insulation and refrigeration technologies.
Furthermore, understanding thermal stratification within the tank is key. Temperature differences can lead to ullage stratification, which affects boil-off rates. Managing pressure is another critical aspect; it helps control gas accumulation and prevents unnecessary tank stress. Utilizing self-pressurization techniques can allow you to take advantage of boil-off gas without incurring additional energy costs.
Transporting liquid hydrogen presents logistical challenges, particularly regarding boil-off gas management. This situation can lead to significant costs due to energy loss and venting needs. As you navigate the complexities of maritime transport, innovative storage solutions become essential to minimize boil-off during long distances.
Regulatory compliance is equally important, ensuring safety in handling and transporting hydrogen.
Frequently Asked Questions
What Are the Safety Measures for Transporting Liquid Hydrogen?
When transporting liquid hydrogen, you need to follow strict safety measures. Always wear protective gear like safety glasses and insulated gloves.
Ensure the vehicle's design includes safety features to handle accidents. Complying with hazardous materials regulations is crucial, as is having emergency procedures in place.
Train all personnel thoroughly on hydrogen properties and safety protocols. Regular inspections are also necessary to maintain compliance and prevent any potential hazards during transport.
How Does Temperature Affect Liquid Hydrogen's State?
Temperature significantly affects liquid hydrogen's state. When you cool hydrogen below its boiling point of 20 K, it remains liquid.
However, if the temperature rises, you'll experience boil-off, as the liquid quickly transitions to gas. This phase change is crucial because liquid hydrogen expands by 845 times when it vaporizes.
Understanding these temperature effects helps you manage storage and transport efficiently, ensuring safety and minimizing losses during transportation.
What Materials Are Used in Hydrogen Transport Units?
Did you know that carbon fiber composites are five times stronger than steel?
In hydrogen transport units, you'll find various materials like these composites, aluminum, and steel, which are essential for durability and efficiency.
Type 3 tanks often use aluminum liners for optimal thermal management, while Type 4 tanks feature lightweight thermoplastic liners.
Fiberglass composites in Type 2 tanks provide a balanced option, ensuring safe and effective hydrogen storage during transport.
Can Liquid Hydrogen Be Stored Long-Term Without Boil-Off?
You can't store liquid hydrogen long-term without experiencing boil-off.
The extremely low temperature required for storage makes it susceptible to heat ingress, leading to vaporization. While advanced insulation and low-pressure conditions can minimize this effect, complete prevention isn't feasible.
If long-term storage is essential, you might want to consider alternatives like ammonia or liquid organic hydrogen carriers, which simplify handling and transport without needing cryogenic temperatures.
What Are the Environmental Impacts of Hydrogen Transport?
Did you know that transporting hydrogen can produce up to 3.5 kg of CO2 for every kg of hydrogen? This highlights the environmental impacts of hydrogen transport, including increased air pollution and greenhouse gas emissions.
You'll also face leakage risks that contribute to climate change and explosion hazards that endanger communities.
Moreover, if you rely on non-renewable energy sources, the resource strain and pollution can be significant, further complicating the hydrogen transport landscape.
Conclusion
In summary, understanding the relationship between internal build and gas boil-off in liquid hydrogen transport units is crucial for optimizing efficiency and safety. As the saying goes, "an ounce of prevention is worth a pound of cure." By addressing these factors proactively, you can minimize unwanted gas emissions and enhance the overall performance of transport systems. Staying ahead of potential issues not only protects your investment but also contributes to a more sustainable future in hydrogen transport.