Wind turbine slip rings prevent wire twisting by enabling smooth power and signal transmission. They are constructed with durable materials like metal-graphite or precious metals and housed in protective aluminum or stainless steel casings. These components play a crucial role in maximizing wind turbine efficiency. If you're curious about how slip rings enhance energy production and support uninterrupted operation, you'll find more valuable information on maintenance, troubleshooting solutions, replacement options, and advanced technologies in slip rings.
Key Takeaways
- Wind turbine slip rings prevent cable twisting.
- Cable untwisting systems counteract tangling.
- Top pulley wheels aid in preventing twists.
- Controllers with electric motors untwist power cables automatically.
- Slip clutch mechanisms prevent motor burnout during untwisting.
Wind Turbine Slip Ring Overview
When it comes to wind turbines, understanding the role and function of slip rings is important for efficient energy production. Wind turbine slip rings are vital components that prevent cable twisting by enabling continuous power and signal transmission between rotating and stationary parts.
Acting as the nervous system of wind turbines, these slip rings guarantee uninterrupted connections for the efficient transfer of wind energy. Constructed with metal-graphite or precious metal brushes and copper/alloy conducting rings, wind turbine slip rings are designed for reliable operation.
The housing of these slip rings, typically made of aluminum or stainless steel, provides protection against environmental factors, ensuring durability and longevity. Despite their small size, wind turbine slip rings play a significant role in enhancing wind turbine efficiency and productivity.
Advantages and Durability of Slip Rings
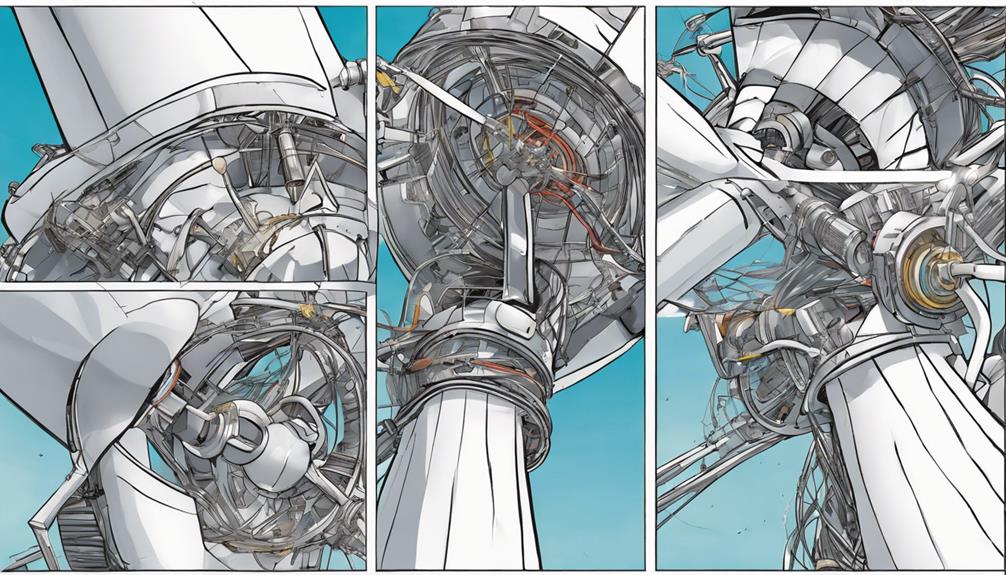
The resilience and reliability of wind turbine slip rings are key factors in maximizing energy production efficiency. Slip rings allow for unlimited 360-degree rotation, enabling continuous alignment with the wind for best power generation.
By ensuring smooth power and data transmission without interruptions, slip rings minimize wear and tear during operation. Their rugged and durable design supports efficient energy conversion, sustaining uninterrupted turbine operation even in harsh weather conditions.
Designed for long-term operation with minimal maintenance requirements, slip rings offer cost-effective maintenance through individual component replacement. The efficiency of slip rings directly impacts wind turbine productivity, underscoring the importance of quality in their design.
With their ability to facilitate seamless rotation and transmission, slip rings play an essential role in the reliable and efficient performance of wind turbines, contributing to their longevity and productivity.
Maintenance and Troubleshooting Solutions
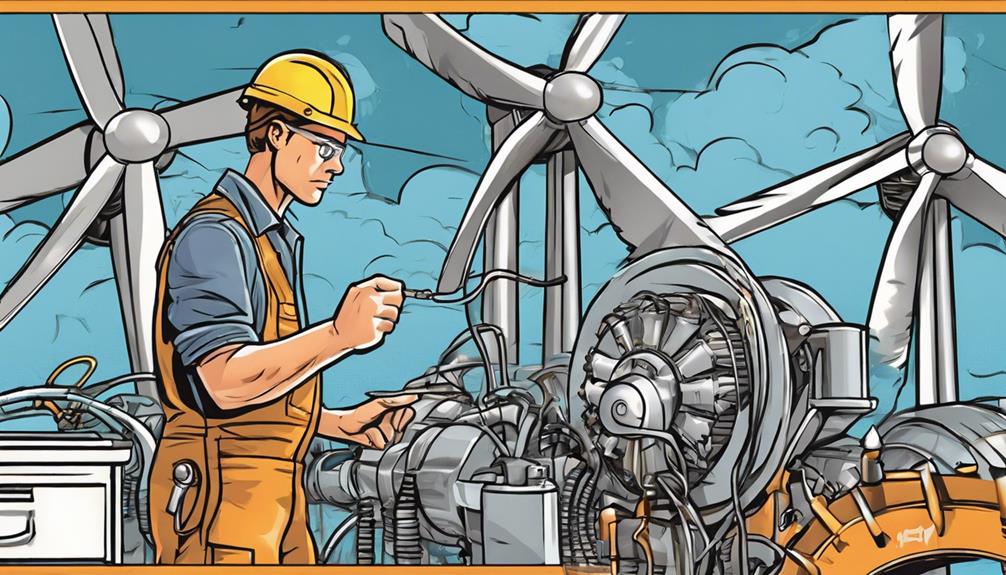
Implementing regular maintenance practices and troubleshooting solutions is vital for preventing wire twisting in wind turbines. By adhering to a maintenance schedule that includes cleaning slip rings, checking connections, and monitoring temperature and voltage levels, you can identify potential issues early on and prevent wire twisting.
Troubleshooting techniques like adjusting brush pressure and addressing electrical noise are essential in maintaining wire alignment and preventing twisting. Additionally, proper maintenance practices such as component replacement and routine cleaning play a significant role in ensuring wire alignment.
Utilizing advanced technologies like slip ring kits and customized solutions can also help maintain wire alignment and prevent twisting in wind turbines. By proactively engaging in maintenance and troubleshooting activities, you can enhance the longevity and efficiency of wind turbine operations while minimizing the risk of wire twisting issues.
Replacement Solutions for Slip Rings
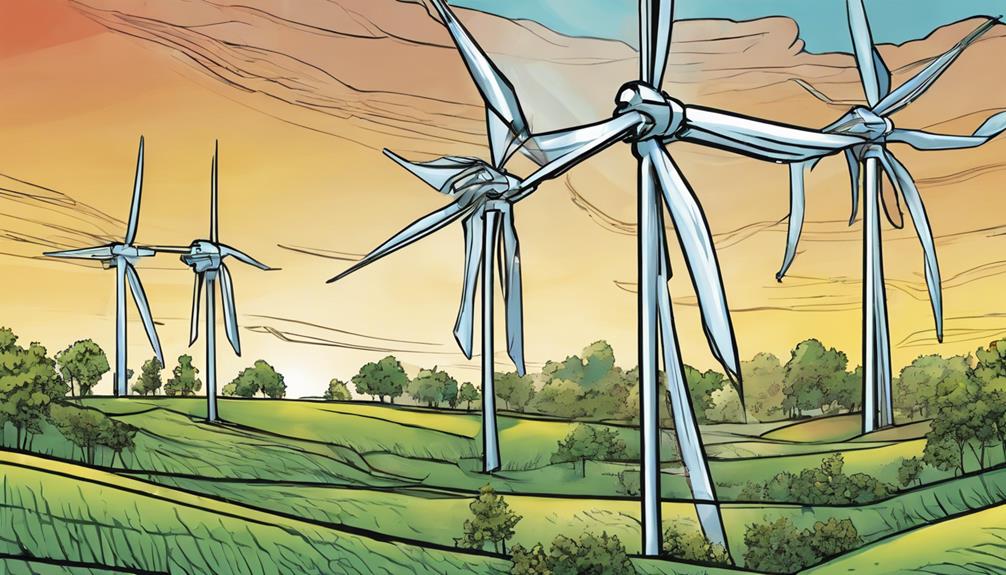
When dealing with replacement solutions for slip rings, it's crucial to focus on maintenance tips such as cleaning brushes and monitoring electrical noise.
Efficient slip ring replacement involves selecting the right part, ensuring proper installation, alignment, testing, and ongoing maintenance practices.
Slip Ring Maintenance Tips
To maximize performance and longevity of slip rings in wind turbines, prioritize regular maintenance tasks such as cleaning brushes and monitoring temperature levels. Guaranteeing that the slip rings are well-maintained can prevent issues like brush wear, contamination, and electrical noise, which may affect the efficiency of the system. Here are some essential slip ring maintenance tips:
Maintenance Task | Description | Importance |
---|---|---|
Clean brushes regularly | Remove debris and dirt to prevent brush wear and guarantee conductivity | High |
Check connections | Inspect for loose connections that can lead to electrical noise | Medium |
Monitor temperature levels | Keep track of temperature to prevent overheating and damage | High |
Inspect for wear and tear | Regularly check for signs of wear on brushes and rings | Medium |
Perform vibration analysis | Identify and address any vibration issues to prevent damage | Low |
Regularly following these maintenance tasks can help in maintaining the efficiency and reliability of slip rings in wind turbines.
Efficient Slip Ring Replacement
Proper slip ring replacement in wind turbines involves identifying and addressing issues such as brush wear, contamination, and electrical noise to guarantee peak performance. When considering slip ring replacement, it's essential to select the right replacement part and verify correct installation to maintain efficiency.
Regular maintenance practices like cleaning, adjusting brush pressure, and component replacement are common replacement solutions for slip rings. Additionally, aligning, testing, and maintaining the replacement part are key steps in optimizing slip ring performance and longevity.
Collaborating with experienced manufacturers for customized solutions can further enhance slip ring efficiency in wind turbines. By adhering to these practices and utilizing tailored replacement solutions, you can make sure that the slip rings in wind turbines operate at their best, minimizing downtime and maximizing energy production.
Installation Process and Customization
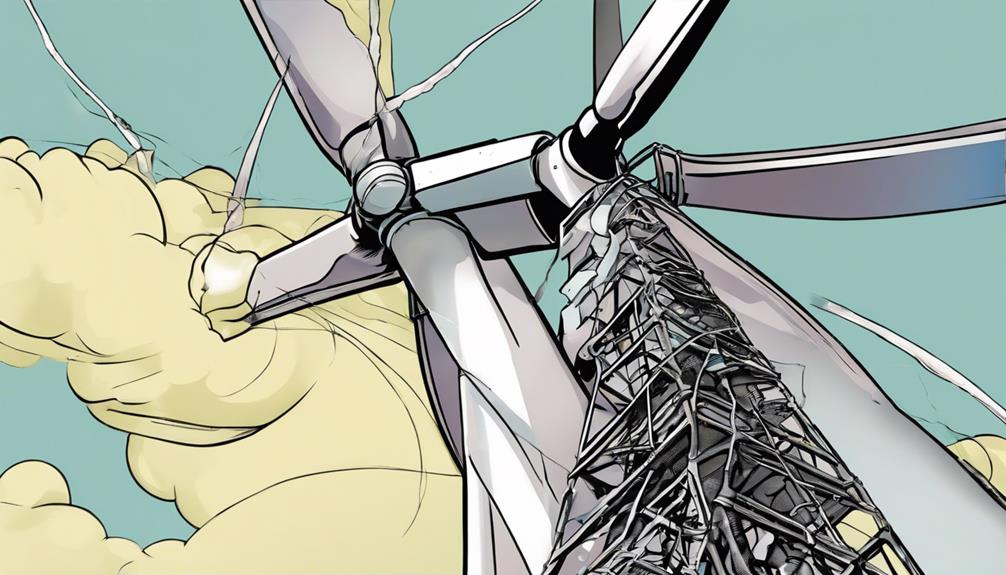
Mounting slip rings on rotating parts is a vital step in ensuring continuous power and signal transmission in wind turbines. The installation process involves customizing slip rings to cater to specific wind turbine designs, ensuring prime alignment and performance while preventing cable twisting.
Proper alignment of brushes and rings during installation is essential to prevent wire twisting and ensure top-notch energy transfer. Customized solutions address environmental challenges and electrical performance requirements, contributing to smooth operation.
By carefully executing the installation process and customizing slip rings, you play a key role in preventing wire twisting and maintaining wind turbine efficiency. Remember, attention to detail during installation ensures that the slip rings function effectively, supporting the overall performance of the wind turbine system.
Prioritize precision and thoroughness in the installation process to guarantee the smooth operation of your wind turbine.
Advanced Technologies in Slip Rings
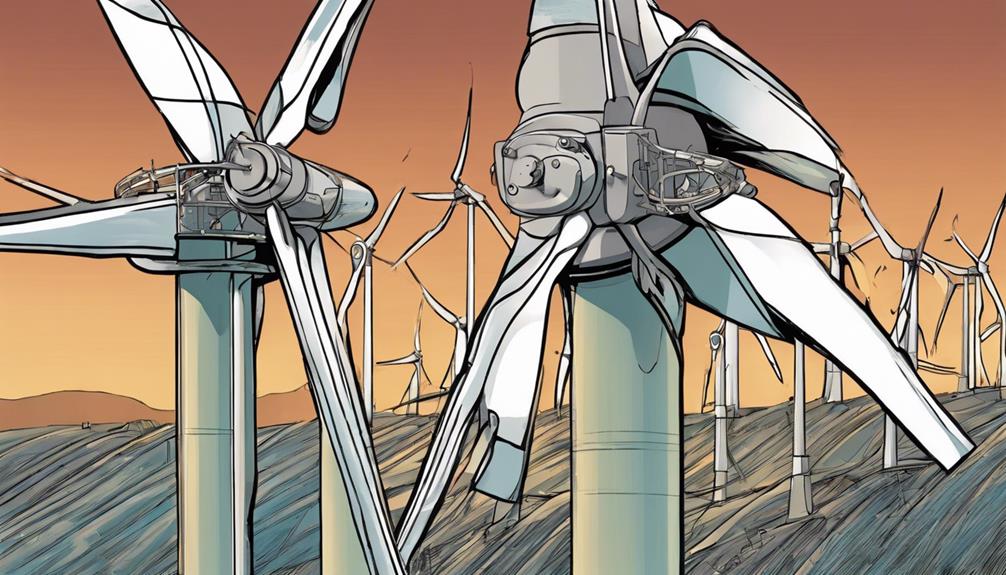
Advanced slip ring technologies, such as Fiber Optic Rotary Joints, transform data transmission rates in wind turbine applications. By incorporating these advanced slip rings, wind turbines can achieve higher data transmission rates, leading to improved overall performance.
The use of Fiber Optic Rotary Joints in slip rings not only enhances data transmission but also reduces maintenance requirements and increases reliability in wind turbine operations. These advancements guarantee smooth power and data transmission without interruptions, optimizing the efficiency of wind turbines.
Moreover, the integration of advanced slip ring technologies contributes to the longevity and sustainability of the entire wind turbine system. Collaborating with experienced manufacturers for customized slip ring solutions can address specific electrical challenges and ensure seamless operation in wind energy generation.
Reputable Slip Ring Manufacturers
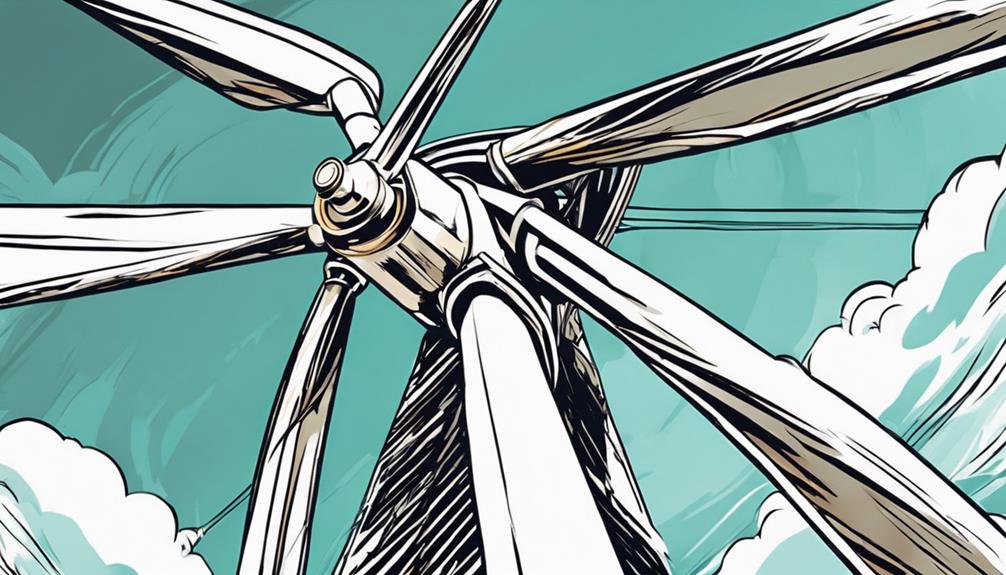
When pondering respected slip ring manufacturers for wind turbine applications, focus on industry leaders like Moog, Schleifring, and Cobham. These companies offer specialized solutions designed to guarantee efficient power and signal transmission in wind turbine systems.
Here are some key factors to ponder when selecting slip ring manufacturers:
- Quality Assurance: Respected slip ring manufacturers adhere to strict quality standards to guarantee reliable performance and durability in wind turbine applications.
- Customization Options: Trusted manufacturers provide customizable solutions tailored to meet specific electrical and environmental requirements, ensuring peak functionality in wind energy generation.
- Longevity and Efficiency: Collaborating with experienced slip ring manufacturers enhances the longevity and efficiency of wind turbines, leading to increased productivity and reduced maintenance costs.
- Industry Expertise: Industry leaders like Moog, Schleifring, and Cobham bring years of expertise and innovation to the design and production of slip rings, offering cutting-edge solutions for wind turbine applications.
Untwisting Wind Turbine Cables
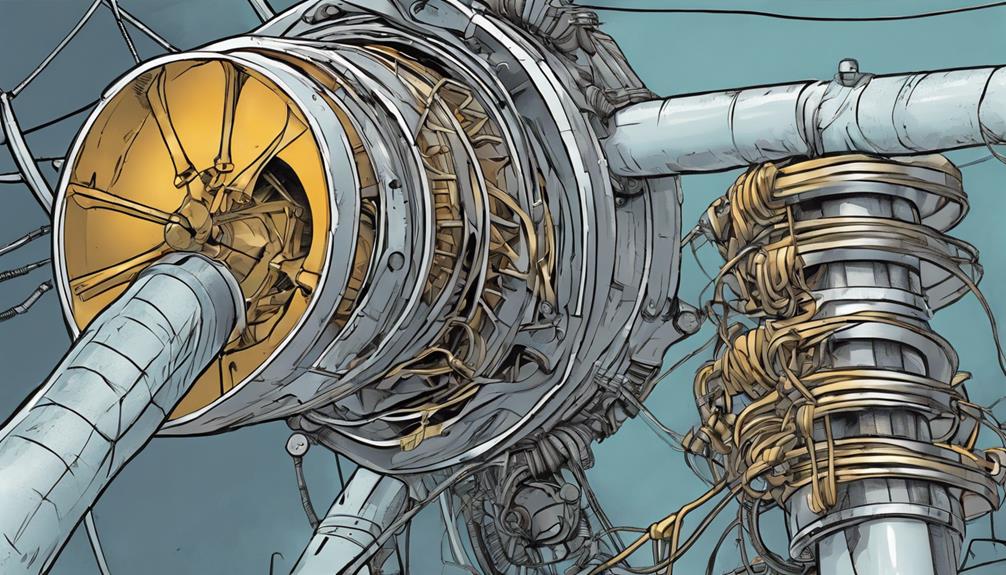
To prevent wires from tangling on a wind turbine, implementing an efficient cable untwisting system is vital. Wind turbines utilize untwisting systems featuring a top pulley wheel that helps counteract cable tangling. These systems often include controllers equipped with electric motors that automatically untwist power cables when wind speeds decrease to zero.
To prevent motor burnout, slip clutch mechanisms are integrated into the untwisting process, ensuring smooth operation. In cases where manual intervention is needed, technicians can manually untangle the cables, offering a flexible backup solution.
Frequently Asked Questions
What Are the Common Electrical Faults in Wind Turbine?
Common electrical faults in wind turbines include brush wear, contamination, and electrical noise issues. Regular maintenance is essential to detect and address these faults promptly, ensuring peak turbine performance and efficiency. Keep up with inspections!
How Do Wind Turbines Swivel?
To make wind turbines swivel, yaw systems use motors or gears to adjust their direction according to the wind. This alignment maximizes energy production. Proper yaw alignment prevents cable twisting, maintaining efficiency in wind energy conversion.
Why Do Wind Turbines Stop Rotating?
Wind turbines stop rotating to prevent damage and ensure safety. Various factors like high winds or mechanical issues can trigger this. Safety mechanisms and control systems are in place to manage rotation and safeguard the turbine.
Why Is There a Twist in Wind Turbine Blades?
To improve performance, the intentional twist in wind turbine blades optimizes aerodynamics and controls lift distribution. Variable blade pitch angles adjust for different wind conditions, maximizing energy capture and turbine efficiency while minimizing stress.
How Does the Twisting of Wind Turbine Blades Prevent Wire Twisting?
The twisting of wind turbine blades in the wind turbine blade design understanding helps to prevent wire twisting. By allowing the blades to twist and adapt to changing wind conditions, the risk of wires getting tangled or twisted is greatly reduced. This design feature ensures the efficient and safe operation of the turbine.
Conclusion
You now have the knowledge and tools to prevent wire twisting on your wind turbine. By utilizing slip rings and following the maintenance and troubleshooting solutions provided, you can guarantee the smooth operation and longevity of your turbine.
Remember, proper installation and customization are key to untwisting those cables and keeping your wind turbine running efficiently for years to come. So, take action now and enjoy the benefits of a well-maintained wind turbine system.