For the most efficient wind turbine blade design, focus on aerodynamics, materials, and modern technologies to boost energy production. Factors like airfoil shape, twist, and strong materials greatly impact performance. Advanced materials like SiC/SiC composites and thermal coatings enhance durability and efficiency. Innovative techniques like Bend-Twist-Coupled Blades and Flatback Airfoils optimize energy extraction. Optimized design through aerodynamic considerations and structural enhancements can further refine efficiency and power output. Gain insights into maximizing turbine blade effectiveness and performance for high-quality energy generation.
Key Takeaways
- Curved blades optimize lift for increased rotational speed.
- Tapered blades reduce stress and enhance structural integrity.
- Twisting blades improve aerodynamics and minimize drag.
- Optimal tip speed ratio maximizes energy extraction.
- Innovative designs like Bend-Twist-Coupled Blades enhance efficiency.
Turbine Blade Basics
Turbine blades, essential components in both gas turbine engines and steam turbines, are radial aerofoils designed to extract energy from high-temperature, high-pressure gas or steam. In the domain of wind energy, efficient blade design is paramount for maximizing power generation.
The aerodynamic design of turbine blades is essential in harnessing wind energy effectively. Rotor blade lift, generated by the shape and angle of the blades, is fundamental in converting wind energy into rotational motion to drive the turbine.
Efficient wind turbine blades are meticulously crafted to optimize energy extraction from the wind. The design of these blades considers factors such as airfoil shape, twist distribution along the blade length, and the number of blades in the rotor.
Turbine Blade Materials
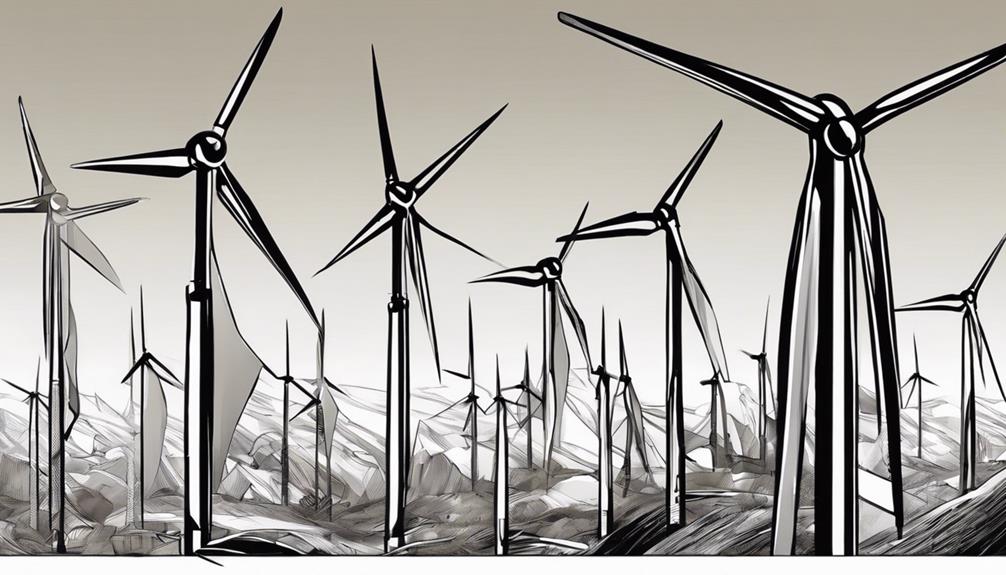
You should consider the advanced nickel-based superalloys commonly used in turbine blade construction, incorporating elements like chromium, cobalt, and rhenium for enhanced durability under high temperatures and stress.
Methods such as directional solidification and single crystal production are employed to bolster blade strength against fatigue and creep, ensuring longevity and performance.
Additionally, the development of Ceramic Matrix Composites (CMC), like SiC/SiC composites, offers lightweight properties and high-temperature resistance, promising advancements in turbine blade materials.
Advanced Blade Materials
Utilizing advanced materials in wind turbine blades enhances their strength and resistance to high temperatures, ensuring top-notch performance under demanding operating conditions. Advanced turbine blade materials, such as nickel-based superalloys, are fortified with elements like chromium, cobalt, and rhenium to provide exceptional strength and heat resistance. Techniques like directional solidification and single crystal production further bolster turbine blade durability against fatigue and creep. Innovations like Ceramic Matrix Composites (CMC), including SiC/SiC composites, are being explored for their lightweight properties and high-temperature capabilities. Additionally, the application of thermal barrier coatings plays a vital role in enhancing corrosion and oxidation resistance, potentially doubling the lifespan of turbine blades. These advancements in materials and designs reflect the continuous effort to balance performance requirements with the challenging conditions faced by gas turbine engines and power plants.
Advanced Blade Materials | Features | Benefits |
---|---|---|
Nickel-Based Superalloys | Superior strength | High-temperature resistance |
Directional Solidification | Enhanced durability | Fatigue and creep resistance |
Ceramic Matrix Composites | Lightweight properties | High-temperature capabilities |
SiC/SiC Composites | Improved heat resistance | Potential for enhanced performance |
Thermal Barrier Coatings | Corrosion and oxidation resistance | Increased turbine blade lifespan |
Material Enhancements Overview
Enhancing turbine blade materials involves incorporating nickel-based superalloys, directional solidification techniques, and Ceramic Matrix Composites to improve performance and durability in demanding operational environments.
Nickel-based superalloys, enriched with elements like chromium, cobalt, and rhenium, enhance blades to withstand high temperatures. The use of directional solidification and single crystal methods strengthens blades against fatigue and creep, essential in gas turbine designs.
Additionally, Ceramic Matrix Composites, such as SiC/SiC composites, offer lightweight properties and high-temperature capabilities, ideal for turbine blades subjected to extreme conditions. Thermal barrier coatings further extend blade lifespan by enhancing resistance to corrosion and oxidation challenges.
Gas turbine configurations, like twin-spool designs, specifically benefit high-pressure turbine blades exposed to hotter, high-pressure air for efficient power generation. Incorporating these material enhancements guarantees turbine blades can operate effectively and endure harsh operational demands.
Impact of Material Selection
Nickel-based superalloys, along with advancements like chromium, cobalt, and rhenium, impact turbine blade efficiency and durability to a large extent. The selection of materials plays a pivotal role in enhancing performance and longevity. Techniques such as directional solidification and single crystal production are utilized to bolster the strength of turbine blades against fatigue and creep, ensuring operational reliability.
Moreover, the development of Ceramic Matrix Composites (CMC), particularly SiC/SiC composites, offers lightweight properties and high-temperature capabilities ideal for turbine blade applications. These materials are continuously being refined to meet the demanding requirements of modern turbine designs.
Additionally, the application of thermal barrier coatings proves crucial in safeguarding turbine blades against corrosion and oxidation, effectively extending blade life.
The careful consideration of material selection in turbine blade design is essential for achieving optimal performance, durability, and the ability to withstand the extreme conditions present in gas turbine engines.
Turbine Blade Cooling Methods
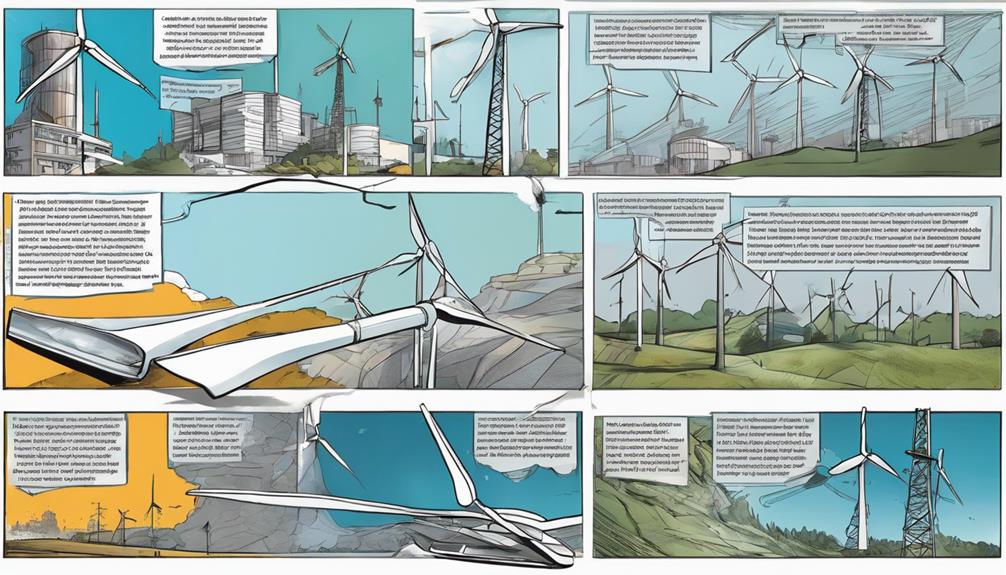
To enhance turbine blade durability and performance, various cooling methods are employed to manage high operating temperatures effectively. Blade cooling methods encompass a range of techniques such as convection cooling, effusion cooling, impingement cooling, and film cooling. These methods play an essential role in balancing cooling efficiency with turbine performance. Technologies like laser-drilled cooling holes and thermal barrier coatings are utilized to enhance the effectiveness of these cooling techniques.
Convection and impingement cooling are internal methods that help regulate blade temperatures, while external methods like film cooling provide additional protection for the blades.
The challenge lies in optimizing these cooling strategies to mitigate the energetic penalty associated with cooling air and to address the complexities in engine design while ensuring temperature compensation for best performance.
Implementing efficient cooling methods is vital to safeguard turbine blades from high temperatures, corrosion, and potential failure modes such as fatigue and creep, ultimately contributing to the longevity and reliability of wind turbine operations.
Turbine Blade Failure Modes
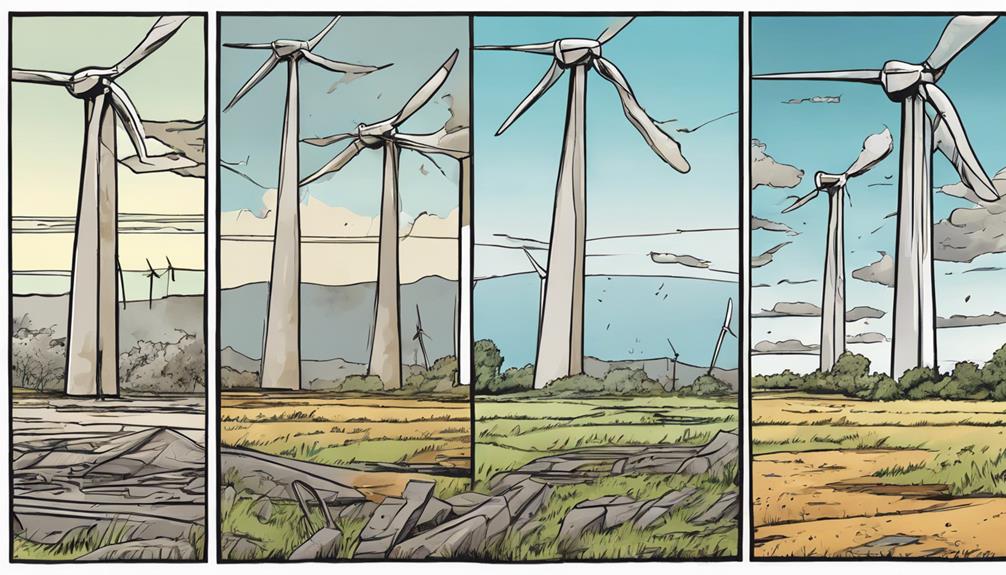
When turbine blades fail, it's often due to a combination of factors such as fracture, yielding, creep, and fatigue, with high temperatures playing an important role in weakening the blades.
Blade fatigue, caused by dynamic stresses, is a common source of turbine blade failure in both steam and gas turbines. To mitigate these failure modes, advanced cooling methods and protection strategies are essential.
Exotic materials like superalloys are utilized to enhance the blades' resistance to fatigue and other stressors. Additionally, techniques such as friction dampers help safeguard against dynamic stresses that can lead to failure.
Cooling methods, including film cooling and thermal barrier coatings, are employed to protect blades from high temperatures and corrosion, ultimately improving their durability and lifespan.
Wind Turbine Blade Designs
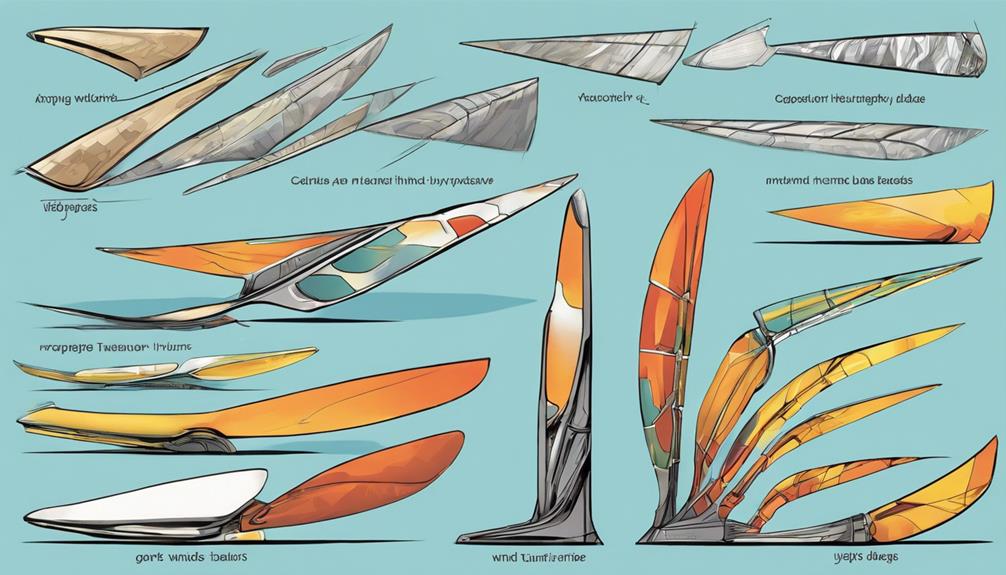
When considering wind turbine blade designs, focusing on factors that enhance efficiency is key.
Analyzing the impact of different designs on performance can lead to optimization techniques for maximizing energy extraction.
Understanding blade efficiency factors is vital for developing wind turbine blades that excel in converting wind energy into rotational motion.
Blade Efficiency Factors
Factors that influence blade efficiency in wind turbine designs include rotor blade length, aerodynamic performance, twisting, and tapering.
Twisted and tapered propeller blades are known to enhance aerodynamics and overall efficiency in wind turbine designs. The use of curved blades, similar to airplane wings, has gained popularity due to their ability to generate lift, subsequently increasing rotational speed for improved energy extraction.
Tapered blades, on the other hand, offer advantages such as increased strength, lighter weight, and better capability to reduce bending stress compared to straight blades within wind turbine designs.
Efficient wind turbine blade design relies heavily on factors like aerodynamic profiles, lift creation, and rotational speeds. Understanding these blade efficiency factors is essential for optimizing wind turbine performance and ensuring effective energy production.
Design Impact Analysis
Blade design significantly influences the efficiency of wind turbines by directly impacting lift, drag, and power generation. Curved blades are designed to generate more lift by leveraging pressure differentials, subsequently increasing rotational speed and enhancing power output.
On the other hand, tapered blades play a pivotal role in reducing bending stress, thereby improving structural integrity and overall efficiency of the turbine. Additionally, twisting the blade along its length is a technique employed to enhance aerodynamics, minimizing drag and contributing to superior performance.
Moreover, optimizing blade design for the tip speed ratio (TSR) is essential for maximizing energy extraction from the wind and ensuring peak efficiency of the turbine system. By carefully considering these design elements, engineers can create wind turbine blades that aren't only efficient but also durable and capable of harnessing the maximum power potential from the wind.
Performance Optimization Techniques
To enhance the efficiency and performance of wind turbine blades, optimizing their design through techniques like twisting and tapering is essential. Blade efficiency heavily relies on aerodynamics, where curved blades create lift by leveraging pressure differences, resulting in increased rotation speed and better energy extraction.
Factors like rotor blade lift, thrust, and tip speed ratio play pivotal roles in determining overall performance. Tapered blades, known for being stronger, lighter, and reducing bending stress compared to straight blades, contribute significantly to improved efficiency.
Advanced technologies such as bend-twist-coupled blades and flatback airfoils are being developed to further enhance blade design for increased power output.
Factors Influencing Efficiency

Enhancing wind turbine blade efficiency relies on various key elements such as rotor blade length, aerodynamic performance, and material composition.
Blade length affects the amount of energy that can be captured, with longer blades generally capturing more energy.
Aerodynamic performance, influenced by factors like twisted and tapered blades, plays an essential role in maximizing energy extraction. Twisted blades vary in angle along their length, optimizing lift generation and rotational speeds. Tapered blades, with a narrower tip than base, enhance aerodynamics, improving overall efficiency.
The tip speed ratio (TSR) is pivotal, as it determines how fast the blade moves relative to the wind speed, impacting energy extraction efficiency.
Material composition is also crucial, affecting the durability and weight of the blades, ultimately influencing performance and maintenance needs.
Blade Design Innovations
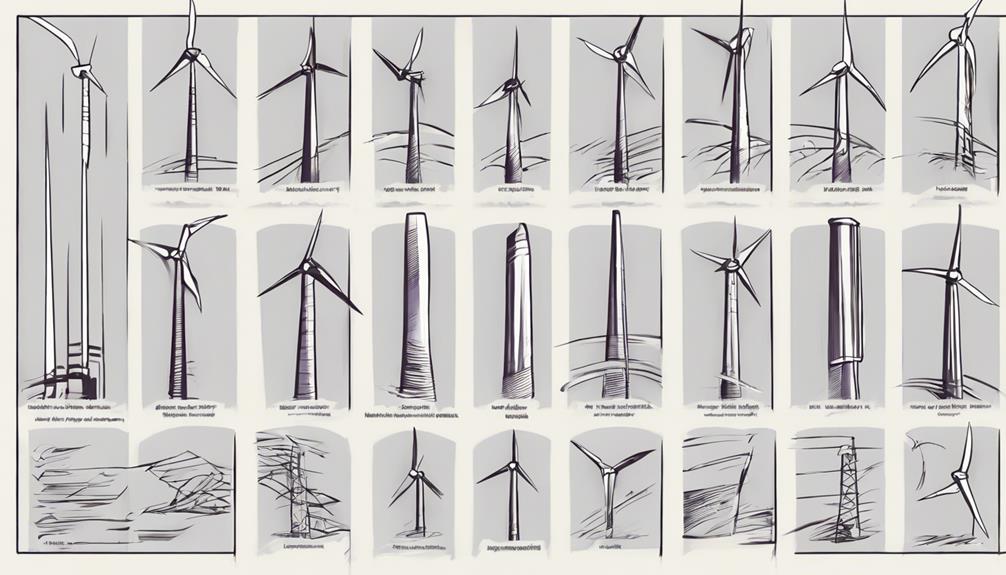
Innovations in wind turbine blade design focus on optimizing efficiency and power output in the field of wind energy technology. Two key advancements in blade design are bend-twist-coupled blades and flatback airfoils. Bend-twist-coupled blades reduce stress on the blades, enhancing aerodynamic efficiency and enabling the construction of longer, lighter blades. On the other hand, flatback airfoils play a pivotal role in optimizing energy production by reducing blade weight while simultaneously improving structural strength.
Blade Design Innovation | Impact on Wind Turbine Technology |
---|---|
Bend-Twist-Coupled Blades | – Reduce stress on blades<br>- Improve aerodynamic efficiency<br>- Enable longer, lighter blades |
Flatback Airfoils | – Optimize energy production<br>- Reduce blade weight<br>- Enhance structural strength |
Laboratory testing has been instrumental in validating these innovative designs, leading to their successful integration into cost-effective commercial production. The adoption of bend-twist-coupled blades and flatback airfoils by the industry has resulted in significant energy-cost reductions and improved performance of wind turbines.
Frequently Asked Questions
Which Blade Design Has the Highest Efficiency for Wind Turbines?
To find the most effective wind turbine blade design, consider curved shapes for lift generation and faster rotation, tapered blades for strength and reduced stress, twisting to minimize drag, and aerodynamic profiles for best energy extraction.
What Is the Most Efficient Shape for a Wind Turbine?
Like a graceful dancer catching the wind's rhythm, the most efficient shape for a wind turbine flows with curved elegance. It harnesses air currents, accelerating energy extraction, and maximizing power generation potential.
What Is the Most Efficient Blade Design?
When it comes to wind turbine blade design, efficiency is key. Curved blades generate lift and rotate faster in the wind, while tapered propeller-type blades with a twist reduce drag and improve aerodynamics for peak performance.
What Are the Most Effective Wind Turbine Blades?
When it comes to effective wind turbine blades, think of them as dynamic air dancers, twisting, curving, and tapering to harness the wind's power efficiently. Modern designs optimize lift, thrust, and speed for maximum energy production.
Does the Angle of the Wind Turbine Blade Affect Its Efficiency?
The optimal angle wind turbine blade plays a crucial role in determining its efficiency. When the blade is positioned at the right angle, it can capture more wind energy, resulting in higher power output. Finding the perfect angle is essential for maximizing the effectiveness of wind turbines.
Conclusion
To sum up, the most efficient wind turbine blade design is one that combines aerodynamic efficiency with lightweight materials.
With advancements in technology, wind turbine blades have become longer and more streamlined, allowing for increased energy production.
In fact, according to a study by the National Renewable Energy Laboratory, longer blades can increase energy output by up to 12% compared to shorter blades.
This highlights the importance of innovative blade designs in maximizing wind energy generation.