Surrogate model-driven multi-objective design in electrical machines is a game changer, streamlining complex processes and reducing costs significantly. These models let you balance efficiency, performance, and cost without extensive simulations. However, challenges like accuracy and nonlinear phenomena must be addressed. By leveraging techniques like Kriging or neural networks, you're equipped to tackle these issues. Discovering hybrid models opens even more possibilities, and you'll find there's much more to explore in this evolving field.
Key Takeaways
- Surrogate models enhance efficiency and reduce computational costs in the multi-objective design of electrical machines, streamlining the optimization process.
- Multi-objective optimization aims to balance design parameters like efficiency, cost, and performance, often utilizing surrogate models to expedite simulations.
- Techniques such as Kriging and hybrid models improve predictive accuracy and flexibility in capturing complex system behaviors in electrical machine designs.
- Challenges include ensuring accuracy and reliability, especially with nonlinear phenomena, necessitating robust validation and error management strategies.
- Future advancements may focus on improving model robustness and exploring broader design variables, addressing current challenges in complex design scenarios.
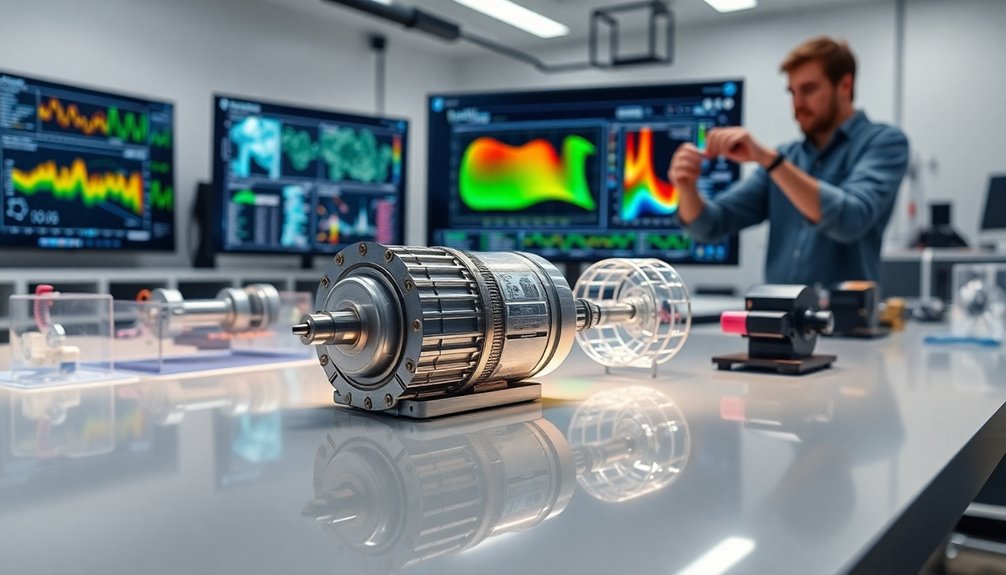
In today's fast-paced engineering landscape, you might find that optimizing electrical machine designs requires not just advanced skills but also innovative approaches. Surrogate models stand out as a powerful tool in this realm, simplifying complex system behaviors to enhance efficiency and reduce computational costs. By approximating intricate dynamics, these models help you save time compared to detailed numerical methods like finite element analysis (FEA).
When you dive into multi-objective optimization, your goal is to balance various design parameters—efficiency, cost, and performance—simultaneously. Surrogate models play a crucial role here, speeding up the optimization process and alleviating the burden of detailed simulations. Techniques like multi-objective evolutionary algorithms (MOEA/D) and genetic algorithms help manage trade-offs between competing objectives, but it's essential to carefully navigate the challenges that arise. Recent advancements in surrogate modeling techniques have further enhanced their applicability in complex design scenarios.
You'll encounter several surrogate model techniques, including Kriging models, Latin Hypercube Sampling, and neural networks. Each method offers distinct advantages for constructing models that can accurately predict outcomes in electrical machine designs.
Hybrid models that combine data-driven approaches with analytical methods are gaining traction, especially when you're working with limited training datasets. These models provide flexibility, allowing you to explore a broader range of design variables without extensive computational resources.
However, accuracy and reliability remain critical challenges. Nonlinear phenomena, such as cogging torque, can be particularly tough to predict. To address this, incorporating physical insights and employing validation techniques can enhance the robustness of your surrogate models.
It's vital to manage errors effectively to ensure reliable predictions.
Frequently Asked Questions
How Do Surrogate Models Compare to Traditional Design Methods?
Surrogate models offer several advantages over traditional design methods. They significantly reduce simulation time, allowing you to iterate faster and explore designs more thoroughly.
With the ability to handle complex systems and multiple objectives, you'll find innovative solutions that may be missed with conventional approaches. While they require quality data and some expertise, the accuracy and predictive capabilities often surpass those of traditional methods, making them a powerful tool in your design arsenal.
What Software Tools Are Best for Implementing Surrogate Models?
When you're navigating the intricate maze of surrogate modeling, pick tools that light your path.
The Surrogate Modeling Toolbox (SMT) shines with its user-friendly Python package and diverse methods like kriging.
For a broader reach, COMSOL Multiphysics integrates advanced models, offering speed and multidimensional interpolation.
Both options empower you to tackle complex problems while minimizing computational time, making your engineering journey smoother and more efficient.
Are There Specific Case Studies in Electrical Machines Using This Approach?
Yes, there are several case studies in electrical machines that utilize surrogate models effectively.
For instance, the Flux-Focusing Halbach Coaxial MG focuses on optimizing performance metrics while reducing torque ripple.
Similarly, five-phase permanent magnet synchronous machines leverage surrogate models for efficient design optimization.
Coreless machines also use surrogate-assisted algorithms to enhance accuracy.
Each study showcases how surrogate models help navigate complex design challenges while minimizing costly evaluations, ultimately improving performance outcomes.
How Can I Validate the Accuracy of a Surrogate Model?
Validating the accuracy of a surrogate model is like tuning a musical instrument; you need precision.
Start by ensuring you collect high-quality data that covers the entire design space. Use common error metrics like Mean Squared Error and Root Mean Squared Error to evaluate the model's performance.
Employ cross-validation techniques to prevent overfitting, and consider Bayesian optimization for efficient assessments.
Consistency in your data collection will maintain the model's reliability and accuracy.
What Skills Are Needed to Effectively Use Surrogate Modeling Techniques?
To effectively use surrogate modeling techniques, you'll need a blend of skills.
Start with solid statistical knowledge, particularly in regression and hypothesis testing. You should also be proficient in programming languages like Python or MATLAB.
Understanding data handling, including cleaning and visualization, is crucial. Familiarity with optimization algorithms and parallel computing will enhance your modeling capabilities.
Lastly, good communication skills will help you explain complex concepts to diverse audiences.
Conclusion
In conclusion, surrogate model-driven design in electrical machines presents exciting prospects but also notable challenges. Did you know that using surrogate models can reduce design time by up to 70%? This statistic highlights the potential efficiency gains in the design process. However, it's crucial to address the obstacles, such as accuracy and complexity, to fully harness these benefits. By overcoming these hurdles, you can truly revolutionize the way electrical machines are designed and optimized for performance.