Wind turbine blades are incredible engineering marvels designed to capture wind energy efficiently. You'll notice they come in various sizes, often exceeding 400 feet in diameter, weighing up to 26 tons. Made from advanced materials like fiberglass and carbon fiber, these blades balance strength and lightweight performance. The manufacturing process involves precise layering techniques and strict quality control to guarantee durability. Innovations continue to enhance blade performance and sustainability. As you explore further, you'll uncover exciting developments in materials and technologies that promise to shape the future of renewable energy.
Key Takeaways
- Wind turbine blades can weigh between 280 grams and 26 tons, designed for optimal efficiency and durability against harsh environmental conditions.
- Advanced materials like fiberglass and carbon fiber provide strength-to-weight advantages, allowing for longer blades that capture more wind energy.
- The manufacturing process involves strategic layering of materials and thorough quality control to ensure high performance and structural integrity.
- Innovations in blade technology include smart monitoring systems and sustainable materials aimed at reducing environmental impact during production and end-of-life disposal.
- Future trends focus on automation, advanced manufacturing techniques, and recyclable materials to enhance turbine performance and sustainability in wind energy.
Overview of Wind Turbine Blades

Wind turbine blades play an essential role in harnessing wind energy, with their design and materials greatly influencing efficiency and durability. The weight of these blades varies considerably, ranging from 280 grams to 26 tons, depending on their design and size.
You'll find that these blades are primarily composed of composite materials, primarily fiberglass, which is the industry standard thanks to its cost-effectiveness and corrosion resistance. However, carbon fiber is also used, offering a superior strength-to-weight ratio that can enhance performance. As larger blades capture more wind energy, their average rotor diameter reached 418 feet in 2021, making these blades comparable in size to the wingspan of a Boeing 747, showcasing their impressive scale.
Their lifespan typically spans around 20 years, during which they must endure harsh environmental conditions and substantial mechanical stresses.
The manufacturing processes for wind turbine blades involve several critical steps, including mold preparation, layering materials, resin infusion, and quality control inspections. Each step plays a crucial role in determining the blades' performance and longevity.
As the wind blade market continues to grow, projected to reach approximately $34 billion per year, the engineering behind these massive structures remains essential in advancing renewable energy goals and wind energy technology.
Materials Used in Blade Construction
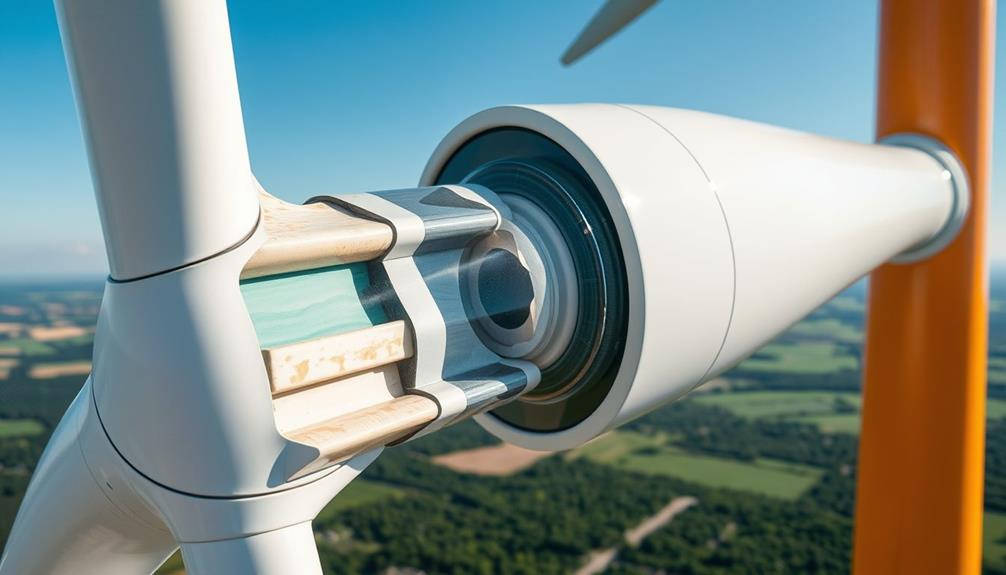
The materials used in blade construction are vital to their performance and longevity. Wind turbine blades primarily utilize composite materials, with fiberglass being the industry standard due to its cost-effectiveness and corrosion resistance. Increasingly, manufacturers are turning to carbon fiber for its superior strength-to-weight ratio, allowing for longer blades that can capture more wind energy.
Here's a quick look at some key materials in blade construction:
Material | Description |
---|---|
Fiberglass | Cost-effective and corrosion-resistant |
Carbon Fiber | Stronger and lighter than fiberglass |
Bio-derived Resins | Eco-friendly and sustainable options |
Wood | Natural material with good properties |
Recycled Materials | Reduces waste and environmental impact |
The combination of different fibers and plastics enhances the blades' durability and performance, much like how rebar strengthens concrete. Additionally, emerging materials focus on sustainability, aiming to minimize the environmental impact of manufacturing. The choice of materials greatly influences the overall costs and performance characteristics associated with wind turbine blades, making this aspect vital for the future of renewable energy.
Manufacturing Process of Blades

When you're involved in the manufacturing process of wind turbine blades, you'll focus on material layering techniques to build strength and durability.
This process is similar to the meticulous engineering behind products like best vacuums for dust removal, where attention to detail is vital for performance.
Quality control inspections play a critical role in ensuring that each blade meets design specifications and performs well over time.
Material Layering Techniques
Manufacturing high-quality wind turbine blades relies heavily on effective material layering techniques. You start with a meticulously prepared mold to guarantee precise dimensions. The process involves strategically layering fiberglass and carbon fiber, which are bonded together with thermoset resins. This combination creates a strong yet lightweight structure that's essential for peak blade performance.
Understanding the importance of budgeting for materials can also enhance the efficiency of the manufacturing process.
As you lay down each layer, you must pay close attention to the alignment of fibers. Variations here can lead to manufacturing inconsistencies that compromise the blade's fatigue life and overall durability. After the initial curing, you'll often add accessories like shear webs and spar caps to enhance the structural stability of the finished product.
At every stage, quality control inspections are critical. These inspections help you identify and rectify potential flaws that could jeopardize the integrity and longevity of the blades.
Quality Control Inspections
Quality control inspections play an essential role in guaranteeing wind turbine blades meet stringent design specifications and performance standards. These inspections assess critical factors such as fiber alignment, resin mixture consistency, and the absence of flaws introduced during composite manufacturing.
Any imperfections can greatly compromise blade integrity, so it's crucial to catch them early. In industries like precious metals, competitive pricing and transparent fee structure are similarly important to maintain product integrity.
Non-destructive testing techniques are employed during this process to identify potential defects that could lead to blade fatigue or failure over time. This method allows you to inspect the blades without causing any damage, assuring they remain structurally sound.
Variability in composite manufacturing can also pose challenges, as identical conditions don't always guarantee uniform properties. Rigorous quality control measures help address these discrepancies.
Continuous monitoring and improvement of quality control protocols are fundamental. By minimizing variations in blade production, you can enhance the overall performance and lifespan of each blade.
Ultimately, these inspections make sure that the final product not only meets but often exceeds the required performance standards, contributing to the reliability and efficiency of wind energy generation.
Curing and Bonding Processes
Curing and bonding processes are significant steps in producing wind turbine blades that deliver both strength and durability. During these stages, the resin hardens, forming a robust structure from the layered composite materials. Controlled environments are essential for maximizing bond strength and guaranteeing material integrity, much like how cold medications require careful selection for effective relief.
Here are key aspects of the curing and bonding processes:
- Resin Infusion: This process involves saturating composite materials with resin, creating a solid bond necessary for durability.
- Curing Conditions: Temperature and humidity are meticulously controlled to achieve the best curing performance.
- Quality Control: Inspections throughout the manufacturing process confirm that the blades meet design specifications, minimizing potential flaws.
- Structural Integrity Enhancements: Accessories like shear webs and spar caps are added post-curing to bolster the blade's overall strength.
Maintaining consistency during resin mixture preparation and fiber alignment is critical. Variability can lead to inconsistencies in composite properties, negatively impacting the blade's fatigue life and reliability.
Innovations in Blade Technology

As the demand for renewable energy continues to rise, innovations in wind turbine blade technology are essential for maximizing efficiency and sustainability. One notable advancement is the use of lightweight composite materials, such as fiberglass and carbon fiber-reinforced structures. These materials improve strength-to-weight ratios, allowing for longer blades that capture more energy.
This aligns with the growing trend towards sustainability and responsible investing, as investors increasingly seek opportunities that contribute to a greener future.
In the last decade, the average rated capacity of wind turbines has doubled, with future designs expected to exceed 2.5 MW, showcasing these advancements' impact on size and efficiency. Additionally, research into biodegradable materials like bamboo and mycelium aims to create compostable wind turbine blades, reducing landfill waste and environmental impact when decommissioned.
Moreover, automation and 3D printing technologies are revolutionizing blade manufacturing processes. These innovations enhance precision, minimize material variations, and greatly improve blade longevity and performance.
Incorporating advanced heating methods and LED curing techniques further strengthens bonds and boosts curing efficiency, making blades more durable and reliable.
Environmental Challenges and Solutions

With advancements in wind turbine blade technology, it's vital to address the environmental challenges that come with increased production and eventual disposal of these blades.
As the demand for renewable energy grows, the need for effective resource management and sustainable investment strategies, such as those offered by Gold IRAs, becomes increasingly important. The lifespan of these structures is about 20 years, and with over 2 million tons of decommissioned blades projected for U.S. landfills by 2050, sustainable disposal solutions are urgent.
To tackle these challenges, consider the following:
- Recycling options: Current efforts include recycling blades into cement, which cuts carbon dioxide emissions by 27%.
- Composite materials: Made up of 80-90% fiberglass and carbon fiber, these durable materials complicate recycling efforts.
- Innovations in recycling: Companies like Siemens Gamesa are developing inherently recyclable blade materials, aiming for 100% recyclability.
- Renewable energy impact: Effective management of blade waste is vital for maintaining the sustainability of renewable energy.
Future Trends in Wind Energy

As you look to the future of wind energy, you'll notice a focus on innovative materials and advanced manufacturing techniques that enhance turbine performance.
This aligns with the principles of design thinking, which fosters creative problem-solving to drive innovation in engineering.
Automation is also playing a key role in boosting efficiency, making production processes faster and more cost-effective.
These trends are set to revolutionize how wind energy is harnessed and utilized globally.
Innovative Material Development
Innovatively, the wind energy sector is increasingly embracing the development of advanced materials that promise to transform turbine blade manufacturing and sustainability. This shift isn't just about efficiency; it's also about environmental responsibility.
Remarkably, the use of advanced materials in other industries, such as the impact of antioxidants on health, can inspire similar breakthroughs in wind energy. Here are some exciting trends you should know:
- Composite materials like carbon fiber are becoming more prevalent, with usage expected to rise considerably.
- Recyclable epoxy resins are being developed to minimize landfill waste from decommissioned blades, addressing the projected 2 million tons heading to U.S. landfills by 2050.
- 3D printing technology is revolutionizing blade manufacturing by enabling faster production and greater design flexibility, making it easier to create longer and more efficient turbines.
- Emerging technologies, including nanoparticles and LED curing methods, are enhancing the quality of resins, speeding up curing times and improving overall performance.
These innovative material developments are paving the way for a cleaner energy future, where sustainability and efficiency go hand in hand.
As the industry advances, you'll likely see even more breakthroughs that prioritize both performance and environmental stewardship.
Advanced Manufacturing Techniques
The future of wind energy is set to be transformed by advanced manufacturing techniques that prioritize efficiency and sustainability. Techniques like 3D printing are revolutionizing wind turbine blade production, enabling faster production times and greater design flexibility. This innovation helps reduce costs and material waste, making it a win for both manufacturers and the environment.
Moreover, as investors look for stable assets in an unpredictable market, diversification of retirement portfolios is becoming increasingly important, echoing the need for innovative solutions in various industries.
Automation in the manufacturing process plays an essential role, enhancing precision and consistency while minimizing material variations. This greatly improves the overall quality of the blades you rely on for renewable energy.
Additionally, innovations such as advanced heating methods and the integration of nanoparticles boost bond strength and curing efficiency, resulting in blades that are more durable and longer-lasting.
Sustainability is also at the forefront, with the use of bio-derived resins and recycled materials gaining traction in blade manufacturing. This shift aligns perfectly with the industry's goals to reduce environmental impacts associated with traditional composite materials.
As we move forward, you can expect to see longer, more efficient blades that leverage advanced materials, with carbon fiber usage projected to increase considerably, additionally enhancing performance in the wind energy sector.
Automation and Efficiency Enhancements
Automation is reshaping the landscape of wind turbine blade manufacturing, driving significant improvements in efficiency and precision. By integrating advanced technologies, manufacturing facilities are enhancing the quality of blades while reducing costs.
Here's how automation is making a difference:
- Precision and Consistency: Automation minimizes material variations, ensuring that every blade meets stringent quality standards.
- Advanced Heating Methods: These methods improve bond strength in composite materials, resulting in more durable blades.
- Nanoparticles and LED Curing: This technology accelerates resin curing times, enhancing the quality of the composite materials used.
- 3D Printing Technology: It offers faster production timelines and greater design flexibility, allowing for innovative blade designs that optimize performance.
As the wind energy industry continues to focus on process improvements, these automation advancements become essential.
They not only boost efficiency but also allow for scalable production that meets the rising demand for renewable energy.
Embracing these trends means you'll witness a transformation in how wind turbine blades are manufactured, paving the way for a more sustainable future.
Frequently Asked Questions
What Are the Giant Blades in Windmills Called?
The giant blades in windmills are called wind turbine blades. They're made from composite materials like fiberglass and carbon fiber, designed to be both strong and lightweight, maximizing energy capture while minimizing structural stress.
What Is the Engineering Behind Wind Turbines?
Imagine colossal wings slicing through the sky; that's the engineering behind wind turbines. You'll find advanced composite materials shaping their blades, while innovative designs enhance efficiency, capturing nature's breath to generate sustainable energy.
Why Can't We Recycle Wind Turbine Blades?
You can't easily recycle wind turbine blades due to their durable composite materials, high transportation costs, and expensive recycling technologies. With growing decommissioned blades, finding efficient solutions is urgent for environmental sustainability and effective waste management.
Are Wind Turbine Blades Bad for the Environment?
Think of wind turbine blades as fallen giants. While they harness clean energy, their disposal casts a long shadow. You'll find their environmental impact troubling, especially when recycling solutions lag behind the industry's rapid growth.
Conclusion
As you stand beneath the towering windmill blades, you can't help but feel the pulse of innovation in the air. These magnificent structures, like giant wings reaching for the sky, embody the harmony between engineering and nature. With advancements soaring higher and environmental challenges tackled head-on, the future of wind energy shines bright. So, embrace the breeze and watch as these colossal blades spin stories of sustainability, propelling us toward a greener tomorrow. In the face of progress, however, we must also address the issue of windmill graveyard solutions. As older turbines are decommissioned, finding sustainable ways to repurpose or recycle their materials is crucial for minimizing environmental impact. By investing in innovative technologies and practices, we can ensure that the lifecycle of wind turbines remains in harmony with our efforts to create a more sustainable world. From repurposing materials for construction to finding new ways to harness their energy potential, the solutions are within reach.