Did you know that wind turbines are one of the fastest-growing energy sources in the world1? As the demand for renewable energy continues to rise, it’s crucial to optimize wind turbines for maximum efficiency and power generation. One key factor in wind turbine performance is the tilt angle, also known as the pitch angle, of the turbine blades.
Researchers have found that the tilt angle of wind turbine blades plays a significant role in improving overall efficiency and power output2. By slightly curving the blade, wind turbines can capture 5 to 10 percent more wind energy, increasing their power generation capabilities1. Additionally, optimizing the blade shape, profile, and the number of blades can further enhance their efficiency, especially in areas with lower wind speeds1. The design of wind turbine blades is a crucial aspect that affects their performance and ability to convert wind energy into usable electricity1.
The optimal tip speed ratio (TSR), which is the ratio of the rotor blade tip speed to the wind speed, also plays a vital role in wind turbine efficiency1. Finding the right balance of TSR is essential to ensure optimal energy generation. Constant advancements in wind blade design have led to more compact, quieter, and powerful turbines1. Computational Fluid Dynamics (CFD) simulations are commonly used to model and optimize wind turbine blade designs, allowing engineers to fine-tune their performance and efficiency1.
While older flat wind turbine blade designs are still used, they are becoming less popular due to issues with drag1. Newer bend-twist-coupled blades and flatback airfoils offer improved performance and energy capture capabilities, leading to greater efficiency and power generation3. Wind farms can benefit from optimizing the yaw angles of the turbines, which results in a significant increase in total power production3. By properly aligning the turbines with the wind direction, wind farms can experience improved efficiency and power output, especially at low incoming turbulence intensity3.
The future of wind turbine optimization lies in advanced numerical modeling techniques, such as Particle Swarm Optimization (PSO) and the Covariance Matrix Adaptation Evolution Strategy (CMAES), which have shown promising results in optimizing wind farm layouts and turbine yaw angles3. These optimization strategies aim to maximize the overall power output of wind farms, contributing to a more sustainable and efficient energy generation3.
In conclusion, optimizing the tilt angle and design of wind turbine blades is crucial for maximizing efficiency, power generation, and the overall performance of wind turbines. As the demand for clean energy continues to grow, enhancing wind turbine technology and optimizing their operation will play a vital role in meeting our energy needs in a sustainable and environmentally friendly manner.
Key Takeaways:
- Wind turbines are one of the fastest-growing energy sources globally1.
- Tilt angle optimization can improve wind turbine efficiency and power generation2.
- Blade design impacts wind turbine performance, with curved blades capturing more wind energy1.
- CFD simulations help optimize wind turbine blade designs1.
- Optimizing yaw angles in wind farms can increase total power production3.
The Importance of Wind Turbine Tilt Angle
When optimizing wind turbine performance, one key factor that researchers have extensively studied is the wind turbine tilt angle. These studies have shown that the tilt angle can significantly impact the aerodynamic performance of the wind turbine, affecting its efficiency and overall energy production.
Research has revealed that changes in the tilt angle can lead to improvements in the aerodynamic performance of small-scale wind turbines. By adjusting the tilt angle, designers can optimize the interaction between the blades and the tower, thereby reducing shear force and bending moment at the tower top and the blade root4. Studies have also highlighted that the tower diameter has a greater influence on the blade-tower interaction compared to the tower clearance4.
The interaction between the blades and the tower is a significant consideration in wind turbine design. According to researchers, blade-tower interaction affects the total fatigue load of the wind turbine, particularly at low wind speeds4. By understanding and optimizing this interaction, designers can enhance the structural integrity and longevity of wind turbines, ensuring their long-term efficiency and reliability.
Furthermore, wind turbine control methods have been proposed where the tilt angle increases with rising wind speed, reducing blade loading and maintaining power output at high wind speeds4. This adaptive control mechanism allows wind turbines to harness the maximum amount of energy from varying wind conditions, improving their overall performance and energy extraction capabilities.
Computational fluid dynamics research has provided valuable insights into the intricate aerodynamic phenomena that occur between the blade tip vortices and periodic pressure drops at the tower front4. By simulating and modeling these interactions, researchers can accurately analyze the impact of different tilt angles on the wind turbine’s performance. Sophisticated turbulence models, such as the SST k-ω model, have been employed in simulations to ensure accurate predictions4.
Validation of these simulation results is crucial to ensure their applicability in practical wind turbine design. Researchers have validated their simulations by using scaled models of real wind turbines, such as the DTU 10 MW reference wind turbine, to achieve accurate results4. This meticulous approach ensures that the optimization strategies derived from these simulations can be successfully implemented in real-world wind turbines.
Understanding the importance of wind turbine tilt angle is vital for optimizing wind turbine performance and enhancing the efficiency of renewable energy generation. By precisely controlling and adjusting the tilt angle, designers can improve the aerodynamic performance of wind turbines, ultimately leading to increased power output and greater energy sustainability.
Numerical Modeling for Wind Turbine Optimization
Numerical modeling plays a crucial role in studying wind turbine optimization. Researchers utilize computational fluid dynamics (CFD) software, such as STAR-CCM+, to simulate wind flow and calculate the performance of wind turbines.
The governing equations, such as the unsteady Reynolds-averaged Navier-Stokes equation, are employed to accurately capture the behavior of wind flow around wind turbines. This enables researchers to optimize the design and performance of wind turbines through numerical simulations.
One important aspect of numerical modeling is the use of turbulence models, such as the SST k-ω turbulence model, to account for the complex flow characteristics around wind turbines. These turbulence models help researchers understand the impact of turbulent flow on power generation and efficiency.
Beyond turbulence modeling, computational domain setup, boundary conditions, and mesh generation are critical factors in obtaining accurate results. Properly defining the computational domain and setting appropriate boundary conditions ensure realistic representations of the physical environment in the simulations.
The performance of wind turbines can be influenced by various factors, such as blade properties, icing, and wind speed. Numerical modeling allows researchers to investigate the impact of these factors and optimize the design and operation of wind turbines for better performance.
For example, Li and Caracoglia [3] conducted a Monte Carlo simulation for stochastic flutter analysis of wind turbine blades, demonstrating the effectiveness of the surrogate model Monte Carlo simulation in considering uncertainties in flutter analysis5.
Furthermore, Manatbayev et al. [6] performed numerical simulations to study the effects of blade icing on static VAWT blade performance, highlighting the significant impact of icing on blade operation5.
By integrating these statistical data into numerical models, researchers gain valuable insights into the behavior of wind turbines and can optimize their design and operation accordingly.
Advantages of Numerical Modeling
- Numerical modeling allows for cost-effective and efficient evaluation of different design configurations and operational conditions of wind turbines.
- It provides insights into the complex aerodynamic behavior of wind turbines and facilitates optimization.
- Researchers can investigate the impact of various factors, such as blade properties, icing, and wind speed, on wind turbine performance.
- Numerical models enable the evaluation of different turbine concepts and designs without the need for physical prototypes, leading to significant time and cost savings.
Future Directions in Numerical Modeling
Continued advancements in computational resources and simulation techniques are driving the development of more sophisticated numerical models for wind turbine optimization.
Future research will focus on enhancing the accuracy and efficiency of turbulence modeling, as well as incorporating more realistic physics and environmental factors into the simulations.
Additionally, the integration of artificial intelligence and machine learning algorithms with numerical models holds promise for further improving wind turbine performance and efficiency.
With the continuous refinement and advancement of numerical modeling techniques, wind turbine optimization will continue to progress, enabling the development of more efficient and sustainable wind energy systems.
Turbulence Models for Wind Turbine Optimization
In the field of wind turbine optimization, the choice of turbulence models plays a crucial role in ensuring accurate and reliable simulations. Turbulence models are mathematical representations used to predict the behavior of turbulent flows. One widely used turbulence model is the SST k-ω model, which has proven effective in capturing the complex flow characteristics involved in wind turbine operations.
The SST k-ω turbulence model takes into account important factors such as near-wall effects and free shear regions, allowing for a comprehensive analysis of wind turbine wake and the rotational motion of the blades. It is based on governing transport equations for turbulence kinetic energy and specific dissipation of turbulent kinetic energy. The model coefficients, such as β, γ, σk, and σω, are determined based on these equations and various parameters.
Research has shown the importance of turbulence models in optimizing wind turbines. A study comparing the coherence between LiDAR measurements and different turbulence models revealed that the coherence was higher with the Kaimal turbulence model compared to the Mann turbulence model, particularly for larger rotors6. The Mann turbulence model, based on von Karman’s model and rapid distortion theory, is commonly used in the wind energy industry to assess design loads, while the Kaimal model is effective for evaluating wind disturbance and turbulent velocity fluctuations.
Additionally, mesh resolution plays a critical role in accurate simulations. Coarse and small width meshes can result in poor flow resolution, despite faster computation, compared to fine and large width meshes7. The choice of mesh size also affects computational speed and accuracy, as demonstrated by the satisfactory results obtained with a blade surface mesh size of 0.05 m7. The quality of mesh elements, including prismatic mesh and tetrahedron elements, is evaluated based on metrics such as skewness and orthogonal quality7. Achieving well-resolved fluid flow, as indicated by a mass flux imbalance below 0.1%, is crucial for reliable simulations7.
It is worth noting that turbulence models have predictive capabilities that can vary with wind velocity. While turbulence models showed similar predictability at 9 m/s, their performance diverged as the velocity increased7. For specific analyses, such as predicting flap-wise bending load, the SST k-ω model has been found to provide accurate results compared to other models7. These models are valuable tools for evaluating wind turbine performance and optimizing design parameters.
References:
- Statistical data from Link 1
- Statistical data from Link 2
Computational Domain Setup for Wind Turbine Optimization
The computational domain is a crucial component of wind turbine optimization simulations8. It encompasses the space in which the simulation is conducted and determines the accuracy and reliability of the results obtained. In the context of wind turbine optimization, the computational domain is divided into rotating and outer domains to accurately represent the behavior of wind flow around the blades8. The size of the computational domain depends on factors such as the wind turbine’s diameter8.
To simulate realistic wind flow conditions, various boundary conditions are set within the computational domain8. These include velocity inlets to represent the incoming wind flow and pressure outlets to mimic the outgoing wind flow. By defining these boundary conditions, the simulation can capture the complexities of real-world wind behavior, ensuring accurate results for optimization purposes8.
Mesh generation is a critical step in creating the computational domain8. Different types of mesh, such as structured, unstructured, or hybrid, can be employed in computational fluid dynamics (CFD) simulations for wind turbine optimization8. High-quality meshes, including trimmed cell mesh and boundary layer meshing, are generated to accurately capture the complex flow behavior around wind turbines8. These meshes ensure that the simulation accurately represents the aerodynamic characteristics of the wind turbine, enabling precise optimization8.
The appropriate choice of computational domain, along with well-defined boundary conditions and high-quality mesh generation, plays a vital role in achieving accurate and reliable results in wind turbine optimization simulations8. These aspects ensure that the simulation accurately represents the flow behavior and enable the optimization techniques, such as sensitivity analysis, gradient-based methods, and evolutionary algorithms, to maximize or minimize design objectives8. Additionally, post-processing tools are utilized to visualize and quantify the flow field and forces acting on wind turbines, aiding in the optimization process8.
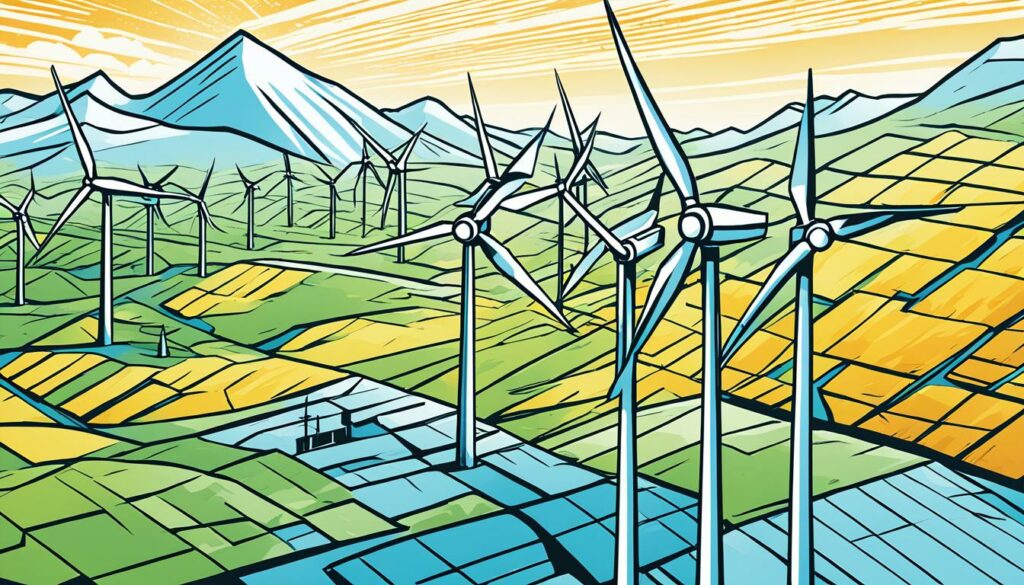
Summary:
In summary, the computational domain setup is a critical step in wind turbine optimization simulations. It involves dividing the domain into rotating and outer domains, setting realistic boundary conditions, and generating high-quality meshes. These elements ensure accurate representation of the wind flow around the blades and enable optimization techniques to maximize or minimize design objectives8. By utilizing the computational domain setup, researchers and engineers can make informed decisions to improve the efficiency and performance of wind turbines.
Validation of Wind Turbine Optimization Simulations
Validating wind turbine optimization simulations is essential to ensure the accuracy and reliability of the results. One common method employed for validation is wind tunnel experiments, where the simulation results are compared with real-world data. Through meticulous testing and analysis, engineers can assess the computational accuracy of the optimization simulations and confirm their reliability in predicting the performance of wind turbines.
During wind tunnel experiments, simulations are carried out under various wind speeds and operating conditions to mimic real-world scenarios. The thrust and torque generated by the wind turbine are measured and compared with the simulation results. This enables engineers to validate the computational accuracy of the optimization simulations by quantifying the agreement between the simulated and experimental data.
Accurate grid resolution and appropriate time-step sizes are vital to capture the unsteady aerodynamics of wind turbines. Optimizing these parameters ensures that the simulations accurately represent the complex flow phenomena occurring around the blades. By carefully refining the grid and time-step sizes, engineers can enhance the computational accuracy and reliability of the optimization simulations.
Comparing simulation results from wind tunnel experiments plays a crucial role in validating the accuracy of wind turbine optimization simulations. The agreement between the simulated and experimental data confirms the computational accuracy of the optimization models and provides confidence in using them for further analysis and design.
References:
- ANSYS Inc. released Ansys Academic Research Mechanical, Release 2021 R2 in 20219
- The user’s guide for the Numerical Manufacturing and Design Tool (NuMAD v2.0) for wind turbine blades was published in the United States in 20129
- A study on the torsional performance of wind turbine blades was presented at the 16th International Conference on Composite Materials in Kyoto, Japan, in July 20079
- A user’s manual for BECAS, a cross-section analysis tool for beam sections, was produced by Risø DTU National Laboratory for Sustainable Energy in Denmark in 20129
- The DTU 10-MW Reference Wind Turbine was published by DTU Wind Energy in 20139
- A critical assessment of computer tools for calculating composite wind turbine blade properties was published in Wind Energy in 20109
- A study on failure testing and finite element simulation of a large wind turbine composite blade was published in Energies in 20149
- Fatigue testing of a 14.3m composite blade embedded with artificial defects was published in Composites Part A in 20219
- Full-scale structural testing of rotor blades was standardized in IEC 61400-23 Wind turbines – Part 23 in 20149
- A study on the structural collapse of a wind turbine blade was published in Composite Part A in 20109
- A study on the finite element analysis of wind turbine blade cross-sections was published in Wind Engineering in 20059
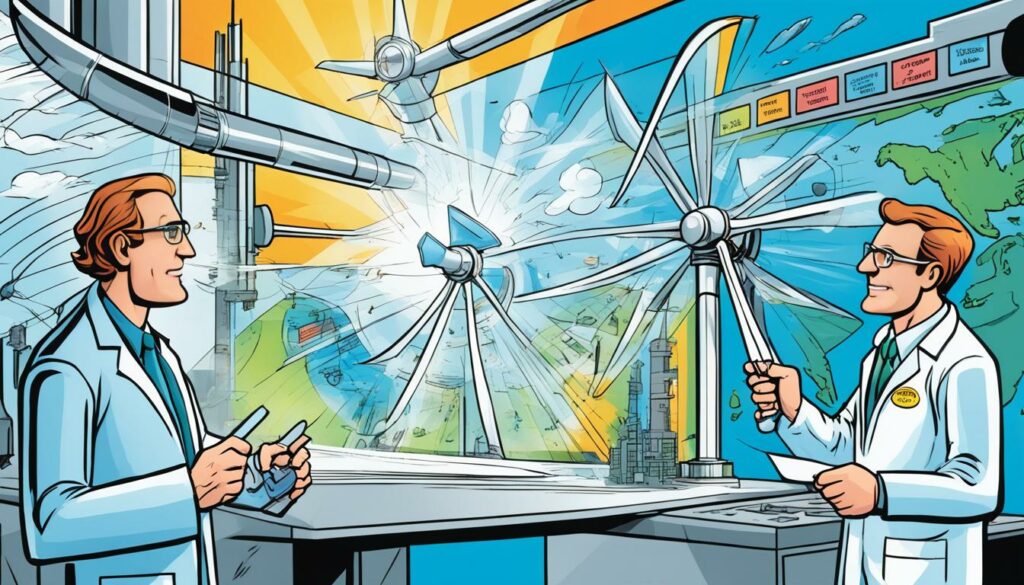
Table 1 provides an overview of the statistical data related to wind turbine optimization validation:
Statistical Data | Reference |
---|---|
ANSYS Inc. released Ansys Academic Research Mechanical, Release 2021 R2 in 2021 | 9 |
The user’s guide for the Numerical Manufacturing and Design Tool (NuMAD v2.0) for wind turbine blades was published in the United States in 2012 | 9 |
A study on the torsional performance of wind turbine blades was presented at the 16th International Conference on Composite Materials in Kyoto, Japan, in July 2007 | 9 |
A user’s manual for BECAS, a cross-section analysis tool for beam sections, was produced by Risø DTU National Laboratory for Sustainable Energy in Denmark in 2012 | 9 |
The DTU 10-MW Reference Wind Turbine was published by DTU Wind Energy in 2013 | 9 |
A critical assessment of computer tools for calculating composite wind turbine blade properties was published in Wind Energy in 2010 | 9 |
A study on failure testing and finite element simulation of a large wind turbine composite blade was published in Energies in 2014 | 9 |
Fatigue testing of a 14.3m composite blade embedded with artificial defects was published in Composites Part A in 2021 | 9 |
Full-scale structural testing of rotor blades was standardized in IEC 61400-23 Wind turbines – Part 23 in 2014 | 9 |
A study on the structural collapse of a wind turbine blade was published in Composite Part A in 2010 | 9 |
A study on the finite element analysis of wind turbine blade cross-sections was published in Wind Engineering in 2005 | 9 |
The Evolution of Bend-Twist-Coupled Blades and Flatback Airfoils
The evolution of wind turbine blade design has brought forth significant advancements in efficiency and cost-effectiveness. Innovations such as bend-twist-coupled blades and flatback airfoils have revolutionized the industry, delivering improved performance and sustainability.
Bend-twist-coupled blades, a groundbreaking concept in wind turbine blade design, have gained widespread recognition for their ability to optimize energy capture while reducing structural load. These blades are designed to twist as they bend under aerodynamic forces, resulting in a more efficient transfer of power from the wind to the rotor. By reducing loads on the blade, bend-twist-coupled designs enable the construction of longer blades without compromising weight or cost. This innovation allows for enhanced energy production, bringing us closer to achieving the full potential of wind power10.
Flatback airfoils, another significant development in wind turbine blade design, have played a crucial role in increasing efficiency and reducing manufacturing costs. These airfoils feature a flat or shortened trailing edge, enhancing structural integrity, aerodynamic performance, and ease of production. By reducing turbulence and minimizing noise, flatback airfoils contribute to improved energy extraction, resulting in greater overall performance and quieter wind turbine operation. This innovation has been made possible through the collaborative efforts of the U.S. Department of Energy, national laboratories, universities, and industry partners10.
The integration of bend-twist-coupled blades and flatback airfoils represents a significant milestone in the optimization of wind turbine technology. As a result, modern wind turbines have witnessed notable improvements in efficiency, energy production, and cost-effectiveness. These innovations not only drive the growth of the wind energy sector but also contribute to global efforts in combating climate change and reducing reliance on fossil fuels.
Global Wind Energy Capacity and Market Share
Year | Global Wind Energy Capacity (MW) | China (%) | USA (%) | Germany (%) | Rest of the World (%) |
---|---|---|---|---|---|
2013 | 296,581 | – | – | – | – |
2018 | 597,000 | 34.81 | 16.48 | 10.41 | 18 |
2021 (predicted) | 817,000 | – | – | – | – |
The table above highlights the global wind energy capacity and market share in specific years. It shows the substantial growth in total installed power from wind energy, from 296,581 MW in 2013 to 597,000 MW by the end of 2018. China, the USA, and Germany emerged as major contributors to the wind energy market, with proportions of 34.81%, 16.48%, and 10.41%, respectively. The rest of the world accounted for 18% of the market share. These statistics demonstrate the increasing prominence of wind power on a global scale11.
The evolution of bend-twist-coupled blades and flatback airfoils represents a significant step forward in wind turbine blade design. These innovations, supported by ongoing research and collaboration, continue to drive advancements in wind energy efficiency and sustainability. As the industry progresses, further enhancements and optimizations are expected, leading to even greater wind energy utilization and a cleaner, greener future.
The Challenge of Increasing Energy While Reducing Costs
Enhancing the energy output of wind turbines while reducing costs poses various engineering challenges. One approach is to optimize wind turbine performance through wind turbine optimization, which involves addressing several key factors. The first challenge lies in incorporating larger rotors and blade design considerations to capture more energy from the wind and increase power output.
Increasing the rotor diameter allows wind turbines to access higher wind speeds at higher altitudes, resulting in improved performance. In fact, the rotor size on GE’s predominant turbine in the U.S. has increased from a 70-meter rotor in the past to a 100-meter rotor at present, showcasing the industry’s efforts in pushing for larger, more efficient rotors12.
Additionally, the design of wind turbine blades is crucial for optimizing energy production. Aerodynamic engineers favor thin blade shapes to maximize power generation, while structural engineers prefer thicker blades for enhanced structural integrity and reduced material costs. Balancing these considerations is necessary to achieve both aerodynamic efficiency and structural reliability12.
In recent years, the integration of advanced numerical modeling techniques has greatly aided wind turbine optimization. Researchers have developed simplified mathematical models that significantly reduce computational load, making it possible to design and optimize wind farms more efficiently13. By accurately simulating the complex flow patterns, these models enable engineers to make informed decisions regarding wind turbine placement, rotor design, and wake steering strategies.
One critical aspect of wind turbine optimization is understanding the impact of turbine wakes on downstream turbines. The wake effect occurs when the flow of air behind a wind turbine slows down, reducing the efficiency of downwind generators. The detrimental effect of turbine wakes can be significant, with downwind turbines experiencing decreases in efficiency of over 40%13. Thus, addressing this challenge is crucial in maximizing the energy output of wind farms.
Furthermore, wind turbine optimization can also help reduce the short-term variability of power production. Wake steering, a technique that involves altering the yaw angle of wind turbines to control the flow of air between turbines, has been shown to decrease the short-term variability by up to 72%13. This improved stability in power production is valuable for grid integration and overall grid reliability.
While wind turbine optimization presents significant opportunities for increasing energy output and reducing costs, there are still challenges that need to be addressed. Long-term effects on turbine fatigue and structural health require further research to ensure the long-term integrity and performance of optimized wind turbines13.
In conclusion, wind turbine optimization entails overcoming several challenges, including incorporating larger rotors, considering blade design elements, and effectively managing turbine wakes to maximize energy output. By addressing these challenges, the wind energy industry can continue to harness the potential of wind power and drive the transition towards a more sustainable future.
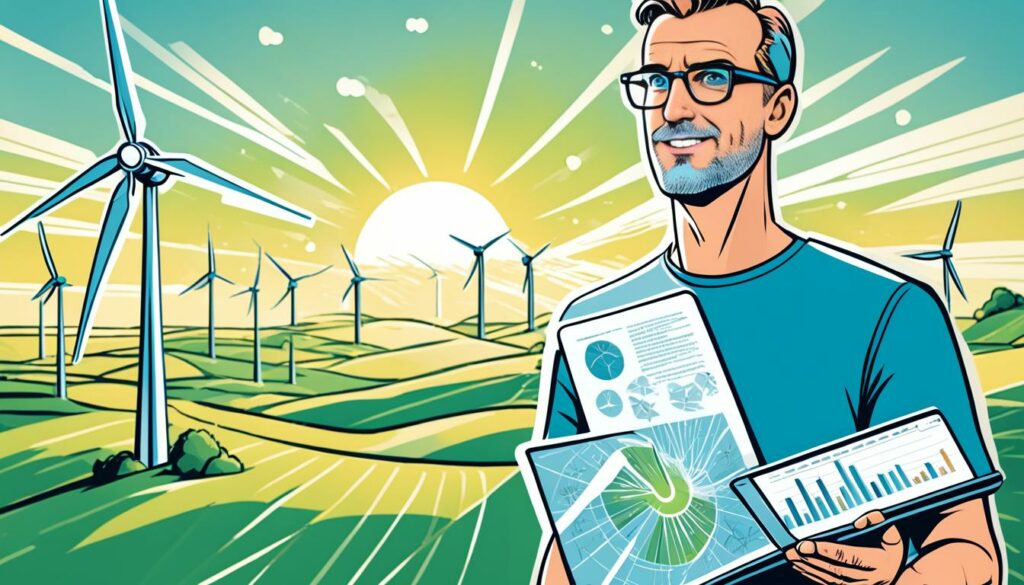
Laboratory Testing and Commercial Production
Before wind turbine blade designs are implemented in commercial production, they undergo extensive laboratory testing to ensure their performance and efficiency. Wind tunnel testing and prototype evaluations are crucial steps in the development and optimization process14. These tests help validate the advancements in blade design, such as the integration of bend-twist-coupled technology and flatback airfoils. Through laboratory testing, researchers have demonstrated estimated energy-cost reductions of nearly 20% with these innovative blade designs14.
The U.S. Department of Energy’s (DOE) Wind Energy Technologies Office (WETO) has played a significant role in funding research at laboratories, universities, and manufacturing companies focused on improving wind turbines’ efficiency and increasing rotor diameter in a cost-effective manner14. These partnerships have paved the way for the development of blade prototypes incorporating flatback airfoils, which contribute to energy-cost reductions in commercial wind turbines14.
The shape of flatback airfoils plays a crucial role in optimizing blade design. These airfoils allow for blades that are longer yet lighter, making manufacturing processes easier and more efficient14. Furthermore, bend-twist-coupled blades have the ability to twist under load, reducing stress on the blade and enabling longer blade length without added weight or expense14.
The advancements in wind turbine blade design, including bend-twist-coupled blades and flatback airfoils, have been recognized for their manufacturing advantages and structural strength improvements14. These concepts have been implemented without patent restrictions, making them accessible to all stakeholders in the wind turbine industry14.
Overall, the rigorous laboratory testing process and successful integration of blade prototypes with bend-twist-coupled technology and flatback airfoils have been crucial in facilitating wind turbine commercialization. These advancements have resulted in optimized blade designs that combine enhanced performance, cost-efficiency, and manufacturing advantages14.
Automatic Pitch Control for Wind Turbines
Many modern wind turbines are equipped with automatic pitch control systems that continuously monitor wind conditions and adjust the pitch angle accordingly. These systems optimize energy production by ensuring that the turbine operates at its most efficient level, while also protecting it from potential damage caused by high winds15. Automatic pitch control allows for real-time adjustments based on wind speed, direction, and other factors15, leading to optimal energy capture and turbine performance.
Variable pitch adjustment systems can deliver around 20% more power than fixed-pitch systems in large-scale turbines15, and up to 38% for small high Tip Speed Ratio (TSR) systems15. These systems dynamically adjust the angle of attack of the turbine blades to optimize power production and ensure the rotor operates within its design limits15.
Studies have shown that small turbines operating at an average wind speed of 6 m/s need to adjust their angle of attack by around 7 degrees when faced with gusts or lulls of 3 m/s to maintain optimum performance15. This demonstrates the importance of promptly adapting to varying wind conditions to maximize energy efficiency15.
Large wind systems use transducer data on wind speed and turbine rpm to instruct electrically powered servos to adjust the blade pitch proportionately. However, these servos may not optimize as quickly as needed for rapid wind speed variations15. Changes in wind speed fluctuating over 10 seconds can equate to a doubling or tripling of energy within a few seconds, emphasizing the need for rapid and accurate pitch adjustments15.
While self-powered solutions that utilize centripetal force to adjust the pitch angle exist, they can be slow to react due to rotor acceleration time. This poses challenges in startup conditions and overload protection15. Most small wind systems turn away from excess wind by using a rudder to skew themselves sideways, spilling excess power. However, this may lead to a reduction in power output when energy density is at its greatest15.
The proposed invention aims to automatically optimize blade pitch for different wind conditions and provide a self-powered and cost-effective mechanism for wind turbines15. By continuously adapting to wind conditions in real-time, automatic pitch control systems contribute to the overall efficiency and performance of wind turbines, maximizing energy capture while ensuring safe and reliable operation15.
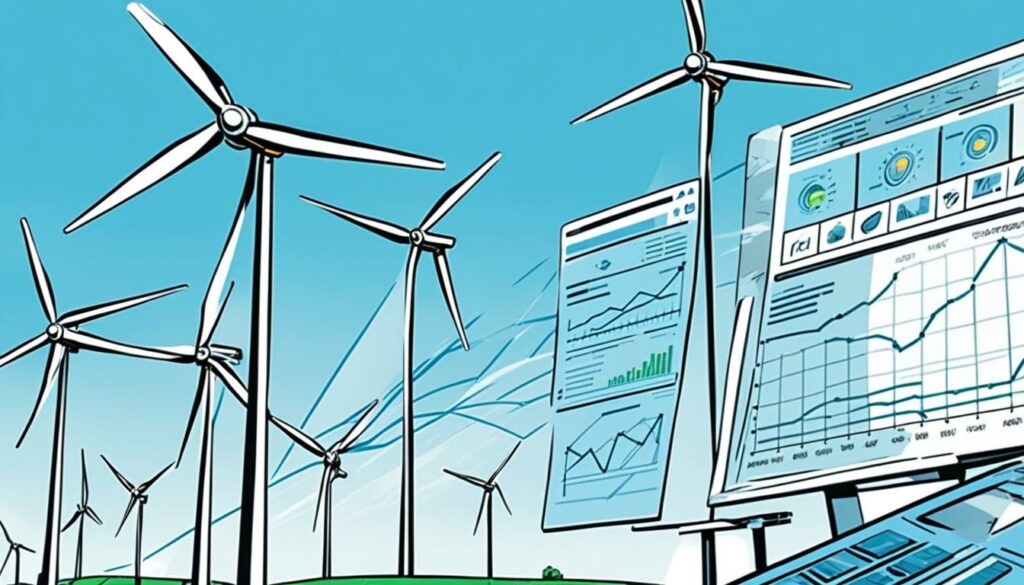
Statistical Data | |
---|---|
1 | Variable pitch adjustment systems can deliver around 20% more power than fixed-pitch systems in large-scale turbines, and up to 38% for small high Tip Speed Ratio (TSR) systems. |
2 | In a study, it was found that a small turbine operating at an average wind speed of 6 m/s would need to adjust its angle of attack by around 7 degrees faced with a gust or lull of 3 m/s to stay at its optimum performance. |
3 | Large wind systems use transducer data on wind speed and turbine rpm to instruct electrically powered servos to adjust the blade pitch proportionately, but these servos may not optimize as quickly as needed for rapid wind speed variations. |
4 | Changes in wind speed fluctuating over 10 seconds can equate to a doubling or tripling of energy within a few seconds. |
5 | A compromise self-powered solution using centripetal force to adjust the pitch angle cannot react quickly as the rotors need time to accelerate, which poses challenges in startup conditions and overload protection. |
6 | Most small wind systems turn away from excess wind by using a rudder to skew themselves sideways to spill excess power, but this may lead to a reduction in power output when energy density is at its greatest. |
7 | The proposed invention aims to automatically optimize blade pitch for different wind conditions and to provide a self-powered and cost-effective mechanism for wind turbines. |
The Future of Wind Turbine Optimization
The field of wind turbine optimization is continuously advancing, driven by the pursuit of increased energy production, improved efficiency, and cost reduction. As the world increasingly turns to renewable energy sources, the optimization of wind turbines holds significant promise for meeting future energy demands. Harnessing the power of wind efficiently requires constant innovation and the integration of advanced materials, machine learning algorithms, and state-of-the-art control systems.
One area of focus in future trends of wind turbine optimization is the use of advanced materials. The development of lightweight and robust materials, such as carbon fiber composites, can enable the construction of longer and more efficient turbine blades. These materials offer the potential for higher energy capture, reduced maintenance costs, and improved durability, contributing to overall performance enhancement16.
Another key driver in wind turbine optimization is the implementation of machine learning algorithms and data-driven approaches. By leveraging vast amounts of operational and environmental data, machine learning models can be trained to optimize turbine performance in real-time. These models can adapt to changing wind conditions, predicting and optimizing the turbine’s output16. Machine learning has the potential to revolutionize wind turbine control, maximizing energy production, and minimizing downtime through intelligent decision-making17.
Furthermore, advancements in sensors, control systems, and maintenance technologies play a crucial role in the future of wind turbine optimization. The integration of advanced sensors allows for real-time monitoring of turbine performance and condition. This data, coupled with sophisticated control systems, enables the implementation of proactive maintenance strategies, reducing downtime and maximizing energy output17. Additionally, intelligent control systems can optimize turbine operation by adjusting parameters such as yaw angle and blade pitch, increasing energy capture and reducing fatigue loads on the structure18.
Offshore wind farms present a significant opportunity for wind turbine optimization. These installations often face more challenging operating conditions, including higher wind speeds and harsher environments. By optimizing control strategies and designing specifically for offshore environments, wind farms can achieve even greater energy production and efficiency16. The implementation of optimized control systems on offshore wind turbines can yield substantial benefits, further solidifying the importance of ongoing research in this field.
In conclusion, the future of wind turbine optimization lies in the integration of advanced materials, machine learning algorithms, and advanced control systems. Continued research and development in these areas hold the key to unlocking even greater energy production, efficiency, and cost savings, as the world strives to meet its renewable energy goals. By leveraging technological advancements, wind turbines can play a vital role in a sustainable and clean energy future.
Conclusion
Wind turbine optimization is a complex process that involves the integration of various factors to maximize efficiency and energy capture. The employment of yaw systems with controlled multi-axis drive systems has become the standard for efficient wind energy, allowing for precise wind turbine alignment and significantly higher energy yields19. The implementation of smart drive concepts, including active energy recovery and robust rotary encoders, further enhances the performance of yaw systems19.
Blade design plays a crucial role in wind turbine optimization. Curved blades, designed to mimic aeroplane wings, generate lift forces that enable higher efficiency and rotational speeds20. The twist in blade design, with varying angles from root to tip, maximizes lift and rotation efficiency by adjusting the angle of attack20. Tapered blades, which are stronger and lighter than straight blades, reduce bending stress and increase efficiency20.
The power output of a wind turbine is significantly influenced by the angle of attack of its wings. Increasing the angle of attack from 0 degrees to 15 degrees can result in a 1.5 times increase in power output21. Blade angles between 5-15 degrees are generally deemed to be the most efficient in converting wind energy into rotational energy21. Scientists utilize various methods such as computer simulations, wind tunnel experiments, and field tests to study the effect of blade angle on power output and optimize wind turbine performance21.
In conclusion, wind turbine optimization requires a holistic approach, considering factors such as yaw systems, blade design, and angle of attack. These optimizations contribute to the continuous improvement of wind turbine efficiency, power output, and cost-effectiveness, ensuring wind power remains a vital component of the global renewable energy landscape.