When it comes to wind turbine efficiency, I've found that optimizing blade weight is key. Even small reductions in weight can greatly boost power output, reduce maintenance costs, and increase the turbine's lifespan. Factors like blade length, shape, and material selection all impact weight, as do design influences like aerodynamic profile and internal reinforcements. Manufacturing processes, such as vacuum infusion and resin transfer molding, also play a role. And let's not forget accessories like fasteners and lightning protection systems. By understanding these factors, I can uncover the perfect balance of weight and performance – and I'm about to dive deeper into the details.
Key Takeaways
- Optimizing blade weight is crucial for turbine performance, as excess weight reduces energy output and increases maintenance costs.
- Material selection and advanced manufacturing processes, like vacuum infusion, can minimize weight while maintaining structural integrity.
- Aerodynamic profile and tip design play a significant role in weight distribution, impacting turbine efficiency and performance.
- Balancing power output and maintenance costs is vital, as weight reduction can compromise structural support and longevity.
- Rigorous testing and simulation are necessary to ensure optimized blade weight and performance without compromising safety and reliability.
Wind Turbine Blade Weight Factors
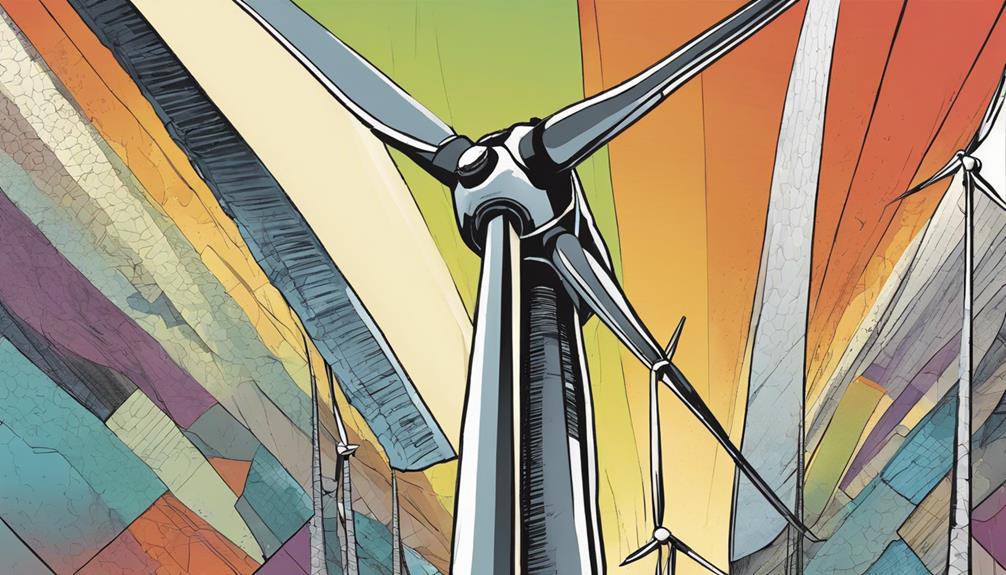
When it comes to wind turbine blade weight, several key factors come into play, including blade length, shape, and material selection, all of which greatly impact the overall weight of the blade.
Longer and wider blades tend to be heavier due to increased surface area, which affects transportation logistics and costs.
Structural support requirements also influence blade weight, as they need to withstand harsh environmental conditions.
In addition, material selection is vital, as high-strength composites like carbon fiber are commonly used to achieve the perfect balance between weight and strength.
Design Influences on Blade Weight
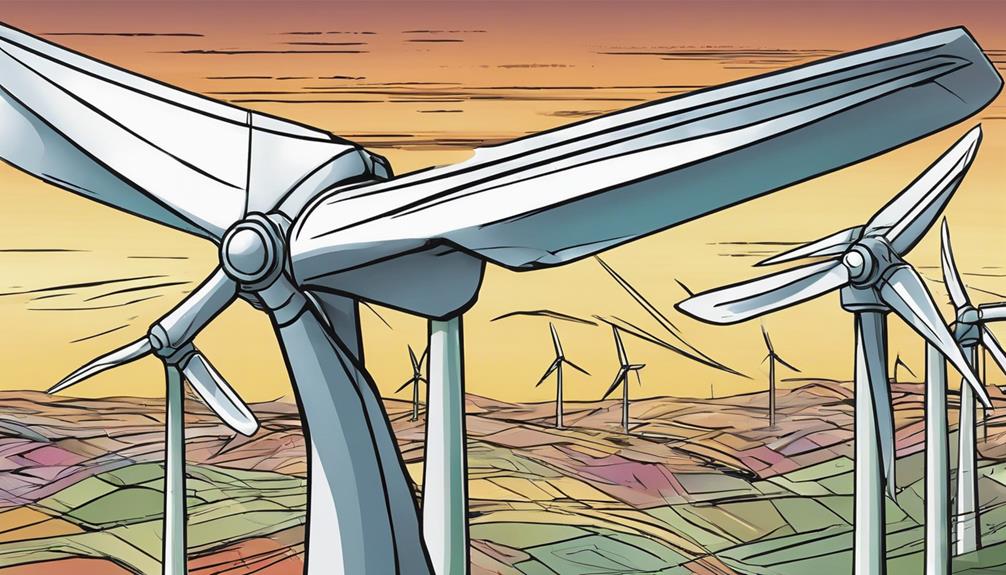
As I explore the world of wind turbine blade design, it's clear that the way blades are shaped and structured has a significant impact on their weight. The length and width of a blade are vital factors, as longer and wider blades tend to be heavier due to increased surface area.
Material selection is also essential, with high-strength composites like carbon fiber being used to minimize weight while maintaining strength. The shape of the blade, including its aerodynamic profile and tip design, also affects weight.
Additionally, structural support requirements, such as the need for internal reinforcements, can add weight to the blade. By carefully balancing these design factors, engineers can optimize blade weight for maximum efficiency.
Optimizing Blade Weight for Performance
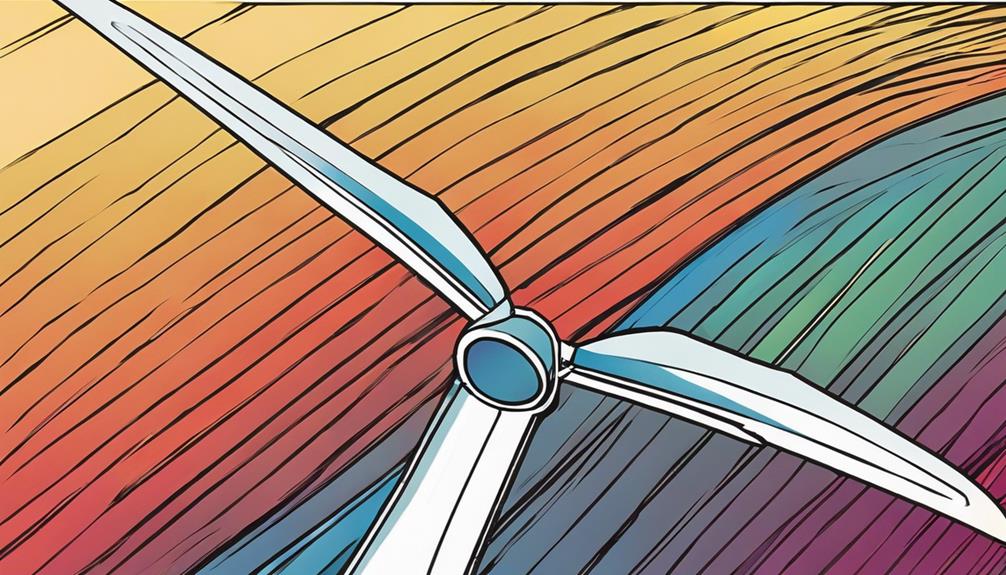
I aim to reduce blade weight while maintaining its structural integrity, acknowledging that every pound shed can significantly impact turbine performance and energy production. Balancing power output and maintenance costs is vital for a greener future.
Efficient energy capture and minimal drag are essential for aerodynamic performance. Rigorous testing and advanced materials are necessary for optimization.
By minimizing blade weight, I can increase turbine efficiency, reduce fatigue loads, and enhance overall performance. This delicate balance requires careful consideration of material properties, structural support, and aerodynamic performance.
Manufacturing Processes and Weight
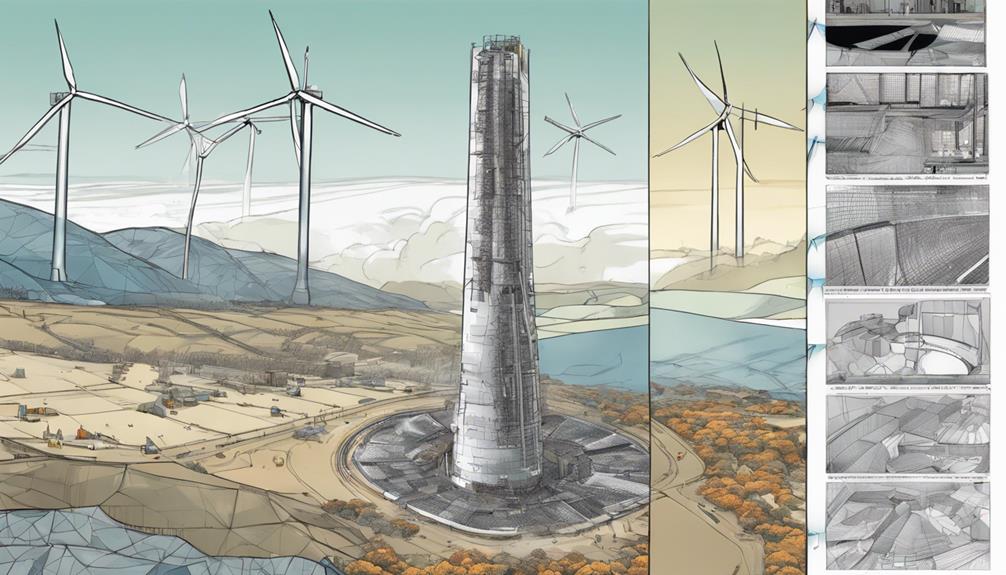
As I explore the world of wind turbine blade manufacturing, I've found that six key manufacturing processes – vacuum infusion, resin transfer molding, and others – impact the final weight and strength of wind turbine blades.
These processes play an essential role in balancing weight and strength, as they determine the density and structural integrity of the blades. For example, vacuum infusion allows for precise control over resin distribution, reducing excess material and minimizing weight.
Meanwhile, resin transfer molding enables the use of lightweight yet strong materials like foam cores. By optimizing these manufacturing processes, we can create blades that are both efficient and durable, ultimately leading to improved turbine performance and reduced maintenance costs.
Accessories and Attachments Impact
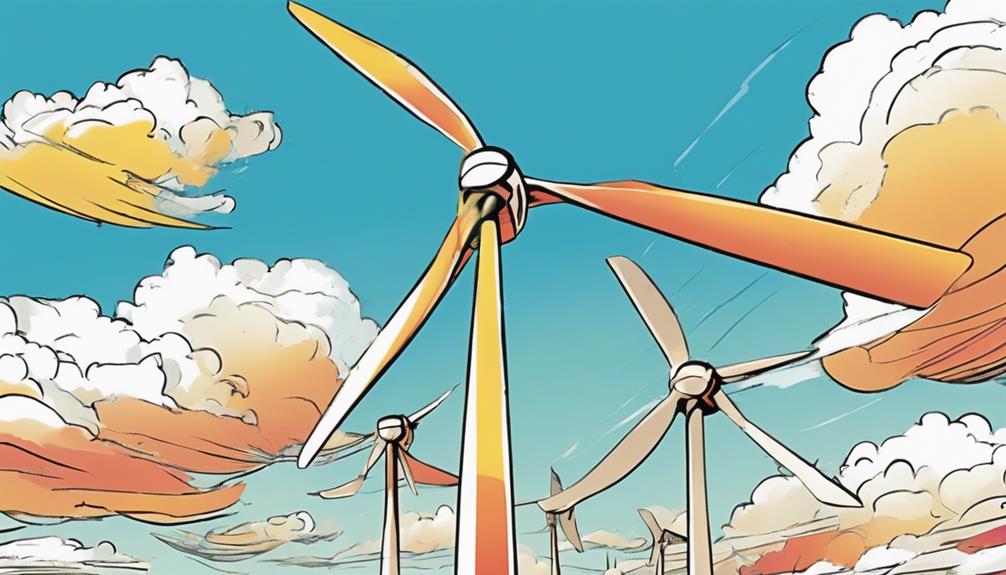
Beyond manufacturing processes, the weight of attachments and accessories also plays a significant role in wind turbine blade design, influencing both aerodynamic performance and structural dynamics. As I investigate the details, I realize that every component contributes to the overall weight of the blade. From fasteners and screws to sensors and lightning protection systems, each attachment impacts the blade's efficiency.
Accessory | Weight Impact | Aerodynamic Impact |
---|---|---|
Fasteners and screws | Moderate | Low |
Sensors | Low | Moderate |
Lightning protection systems | High | High |
Leading edge protection | Moderate | High |
Ice detection systems | Low | Low |
Frequently Asked Questions
How Do Wind Turbine Blades Compare in Weight to Other Industrial Components?
When comparing wind turbine blades to other industrial components, I find they're surprisingly heavy, with some weighing up to 45,000 pounds, rivaling the weight of large construction equipment or even small airplanes.
Can 3D Printing Be Used to Manufacture Wind Turbine Blades?
"I'm exploring the possibility of 3D printing wind turbine blades. While it's theoretically feasible, I'm concerned about scaling up to massive blade sizes and ensuring the printed materials meet performance and durability standards."
Do Heavier Blades Always Produce More Energy?
"I used to think heavier blades meant more energy, but surprisingly, it's not that simple. While larger blades capture more wind, excessive weight can decrease efficiency due to increased drag and structural stress."
What Is the Average Lifespan of a Wind Turbine Blade?
"I've learned that the average lifespan of a wind turbine blade is around 20-25 years, depending on factors like environmental conditions, maintenance, and material quality, which all impact its durability and performance."
Can Blade Weight Be Reduced Without Compromising Structural Integrity?
"I'd say it's a delicate balancing act, but yes, blade weight can be reduced without compromising structural integrity. Advanced materials and clever design tweaks can shave off pounds without sacrificing strength or performance."
How Does Proper Lubrication Affect the Efficiency of Wind Turbine Blades?
Proper lubrication plays a crucial role in optimizing wind turbine performance. When wind turbine blades are effectively lubricated, there is less friction and wear, leading to improved efficiency and reduced maintenance costs. This ensures that the blades can operate at their full potential, generating more clean energy.
What Is the Relationship Between Wind Turbine Blade Selection and Efficiency Optimization?
When it comes to mastering wind turbine blades, the selection process is crucial for optimizing efficiency. The right blade design can significantly impact the performance of wind turbines, affecting factors such as energy output, noise levels, and maintenance requirements. Careful consideration of blade characteristics is essential for maximizing overall efficiency.
What Factors Should Be Considered When Optimizing Wind Turbine Blade Weight for Efficiency?
When it comes to mastering wind turbine blades, optimizing weight is crucial for efficiency. Factors to consider include material strength, aerodynamics, and balance. Choosing the right materials and design can help reduce weight while maintaining structural integrity, ultimately maximizing energy production and minimizing costs.
How Can Wind Turbine Blade Weight Impact Efficiency and Performance?
The weight of optimal wind turbine blades directly affects their efficiency and performance. Heavier blades require more energy to rotate and may lead to increased wear on the entire system. Lighter blades can improve efficiency and reduce strain on the turbine, ultimately leading to better overall performance.
Conclusion
As I reflect on the intricate dance of wind turbine blade design, I realize that optimizing weight is the master key that opens the door to efficiency.
By striking the perfect balance between strength, durability, and weight, engineers can create blades that slice through the air like a hot knife through butter, harnessing the wind's power with precision and finesse.
This delicate harmony is the linchpin to a sustainable future, where wind energy reigns supreme.