Efficient wind turbines depend on best oil care to prevent contamination, reduce downtime, and secure reliable performance. Subpar lubrication practices can lead to costly repairs, environmental harm, and compromised energy production. Regular monitoring, maintenance, and oil changes are essential to prevent oil contamination issues. High-grade oil with proper viscosity, anti-wear, and anti-corrosion properties is crucial for gearbox performance, bearing lubrication, and braking system hydraulic oil. By following turbine reliability best practices, wind turbines can operate effectively and sustainably. To explore the complexities of finest oil care and its impact on wind turbine performance, continue below.
Key Takeaways
- Regular oil analysis and maintenance prevent contamination, ensuring reliable turbine performance and minimizing downtime.
- High-quality lubricants with ideal viscosity, anti-wear, and anti-corrosion properties are crucial for optimal turbine operation.
- Adhering to manufacturer guidelines for maintenance and repair, including timely oil changes, is vital for turbine longevity.
- Proper lubricant selection, cleanliness, and filtration prevent premature bearing failure and reduce maintenance costs.
- Monitoring oil consumption helps evaluate turbine efficiency and sustainability, ensuring optimal performance and environmental responsibility.
Preventing Oil Contamination Issues
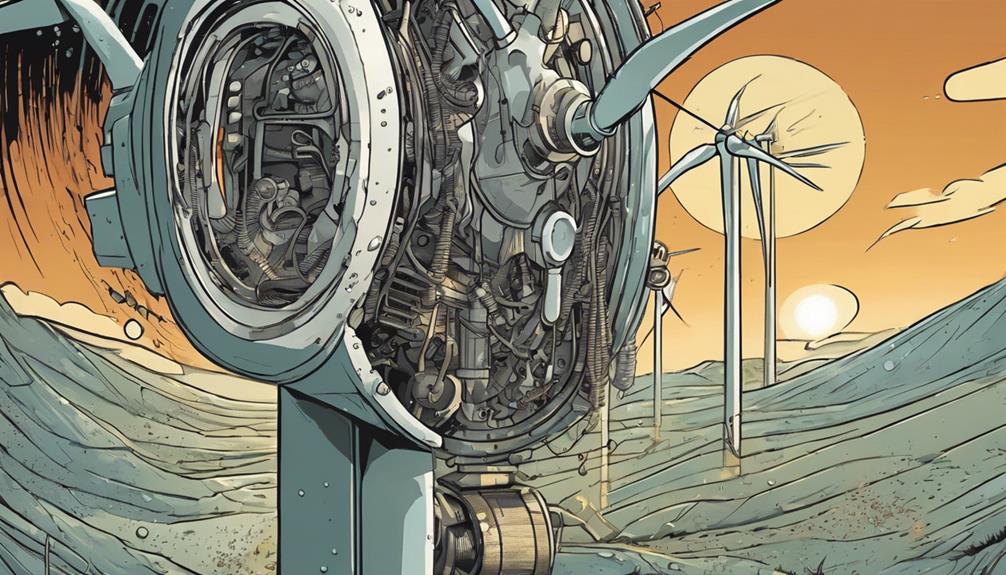
Effectively preventing oil pollution issues in wind turbine systems requires a proactive approach that involves regular monitoring, maintenance, and oil changes to minimize the risk of premature wear, failure, and environmental pollution.
Contaminated oil can lead to costly repairs, downtime, and environmental damage. Regular monitoring of oil quality helps detect potential issues before they escalate. High-quality oil with good viscosity, anti-wear, and anti-corrosion properties is essential for peak performance and longevity of wind turbine systems.
Proper maintenance practices, including timely oil changes, reduce the risk of system failures and breakdowns. By prioritizing oil maintenance, wind turbine operators can ensure efficient, reliable, and environmentally sustainable performance.
Gearbox Performance and Maintenance
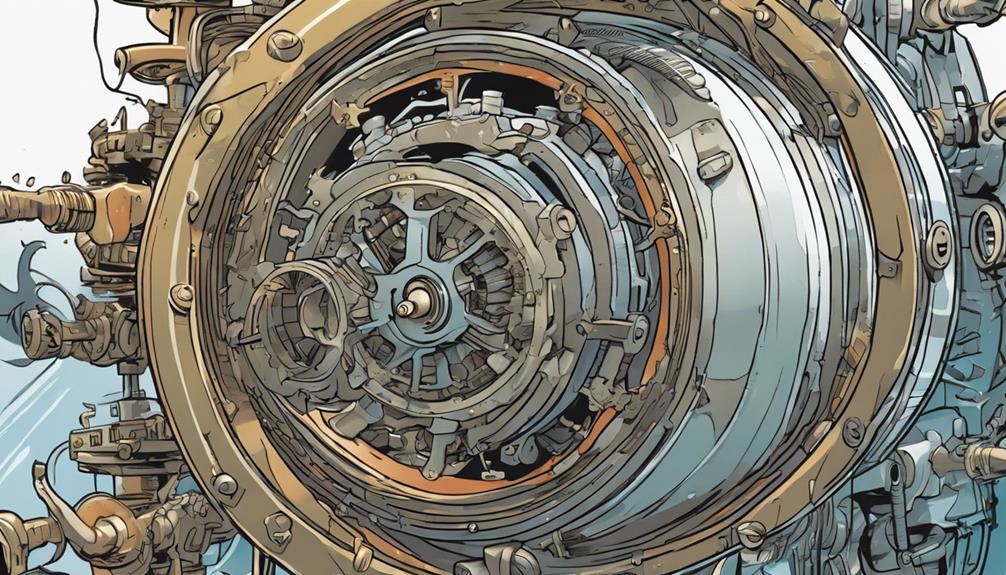
Proper gearbox performance and maintenance are critical components of wind turbine operation, as gearbox failures can lead to extended downtime and significant repair costs. Regular monitoring and maintenance of gearbox oil quality are essential to prevent contamination and premature wear of components.
Here are key considerations for gearbox performance and maintenance:
- Regular oil analysis to detect contaminants and wear metals
- Timely oil changes to prevent contamination and wear
- Proper filtration to remove contaminants and debris
- Regular inspection of gearbox components for signs of wear
- Adherence to manufacturer guidelines for maintenance and repair
Bearing Lubrication Essentials
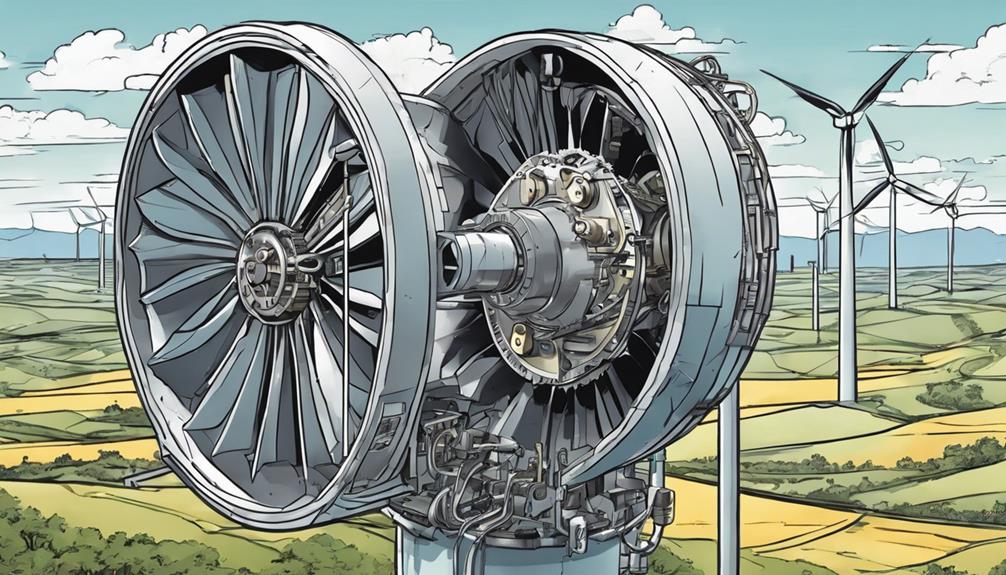
In wind turbines, bearings rely on a thin layer of lubricant to reduce friction and wear, making high-quality oil with ideal thickness and anti-corrosion properties essential for smooth operation and extended lifespan.
Contaminants like dirt and water can lead to premature bearing failure, emphasizing the importance of regular oil analysis and maintenance. Selecting the right lubricant and maintaining cleanliness are key for peak bearing performance.
Proper lubrication ensures that bearings operate within safe temperatures, reducing the risk of overheating and subsequent damage. By adhering to recommended maintenance schedules and using high-quality oil, wind turbine operators can minimize downtime, reduce maintenance costs, and maximize energy production.
Braking System Hydraulic Oil
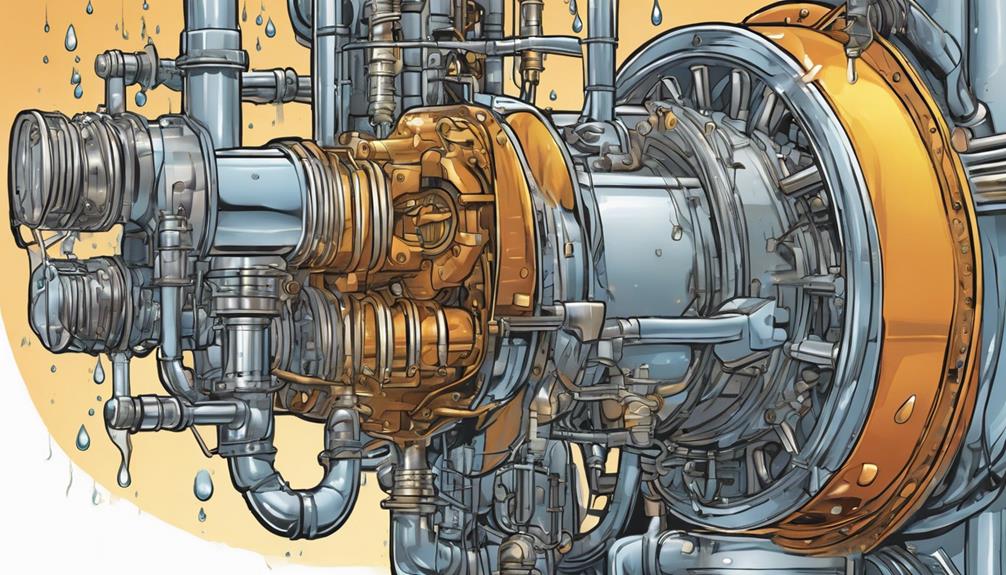
Reliability in wind turbine braking systems hinges on the quality and performance of hydraulic oil, which plays a critical role in maintaining pressure and control. The hydraulic oil guarantees smooth operation and effective braking, preventing catastrophic failures and maintaining the turbine's overall performance.
However, contamination can lead to decreased performance and system failure, emphasizing the importance of regular maintenance and oil changes.
Regular oil changes optimize turbine performance and prevent contamination.
Improper disposal of hydraulic oil can cause environmental pollution.
Monitoring oil quality guarantees system reliability and prevents breakdowns.
High-quality oil reduces friction, heat, and wear on braking system components.
Proper maintenance practices minimize the risk of system failures and malfunctions.
Turbine Reliability Best Practices
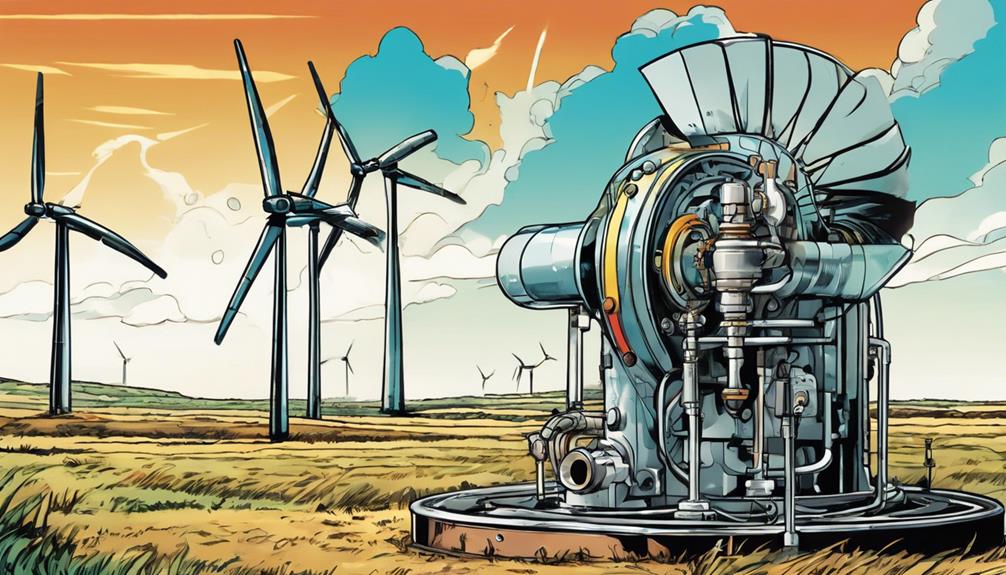
By following a strict maintenance schedule and choosing high-quality lubricants, wind turbine operators can minimize the risk of component failures and enhance overall turbine reliability.
Regular oil analysis and maintenance are essential to prevent contamination and ensure reliability. Proper lubricant selection, timely oil changes, and cleanliness are necessary for best bearing performance. Monitoring oil consumption helps evaluate turbine efficiency and environmental sustainability.
Best Practice | Description | Benefits |
---|---|---|
Regular Oil Analysis | Monitor oil quality and contamination | Identify potential issues before they cause harm |
Timely Oil Changes | Replace oil at recommended intervals | Prevent deterioration on components |
Proper Lubricant Selection | Choose high-quality oil with good viscosity and anti-corrosion properties | Maximize performance and longevity |
Frequently Asked Questions
What Are the Consequences of Ignoring Oil Maintenance in Wind Turbines?
Ignoring oil maintenance in wind turbines can lead to premature wear, component failure, costly repairs, and environmental pollution, resulting in decreased efficiency, increased downtime, and significant financial losses.
How Often Should Oil Filters Be Replaced in Wind Turbine Systems?
Wind turbine oil filters should be replaced regularly, ideally every 6-12 months or as recommended by the manufacturer, to prevent contamination, maintain peak performance, and minimize system failures.
Can Wind Turbines Operate With Non-Synthetic Oil in Extreme Temperatures?
In extreme temperatures, a wind turbine in the Scottish Highlands experienced reduced performance using non-synthetic oil. Synthetic oil's superior viscosity and thermal stability make it a better choice for peak performance in extreme conditions.
What Are the Benefits of Using Bio-Based Oils in Wind Turbine Maintenance?
Bio-based oils offer a sustainable, eco-friendly alternative for wind turbine maintenance, providing similar performance to traditional oils while reducing environmental impact and carbon footprint, making them an attractive option for environmentally conscious operations.
How Does Oil Viscosity Affect Wind Turbine Performance in Cold Climates?
In cold climates, 75% of wind turbine failures are attributed to lubrication issues. Oil viscosity directly impacts wind turbine performance, as low viscosity oils can lead to inadequate lubrication, increased wear, and reduced efficiency in freezing temperatures.
How Can Optimal Oil Maintenance Contribute to the Future of Wind Turbines?
Optimal oil maintenance is crucial for the efficiency and longevity of future wind turbines technology. Regular monitoring and timely oil changes can reduce friction and wear, leading to increased reliability and performance. By prioritizing oil maintenance, we can ensure that future wind turbines technology operates at its full potential for years to come.
Conclusion
To wrap up, the threads of best oil maintenance weave together to form a tapestry of efficiency, reliability, and sustainability in wind turbine operations.
By prioritizing high-quality oil, regular analysis, and proper disposal, wind farm operators can minimize environmental impact, reduce downtime, and maximize energy production.
As the wind energy industry continues to grow, the importance of best oil maintenance will only continue to spiral upward, much like the turbines themselves, reaching for the sky.